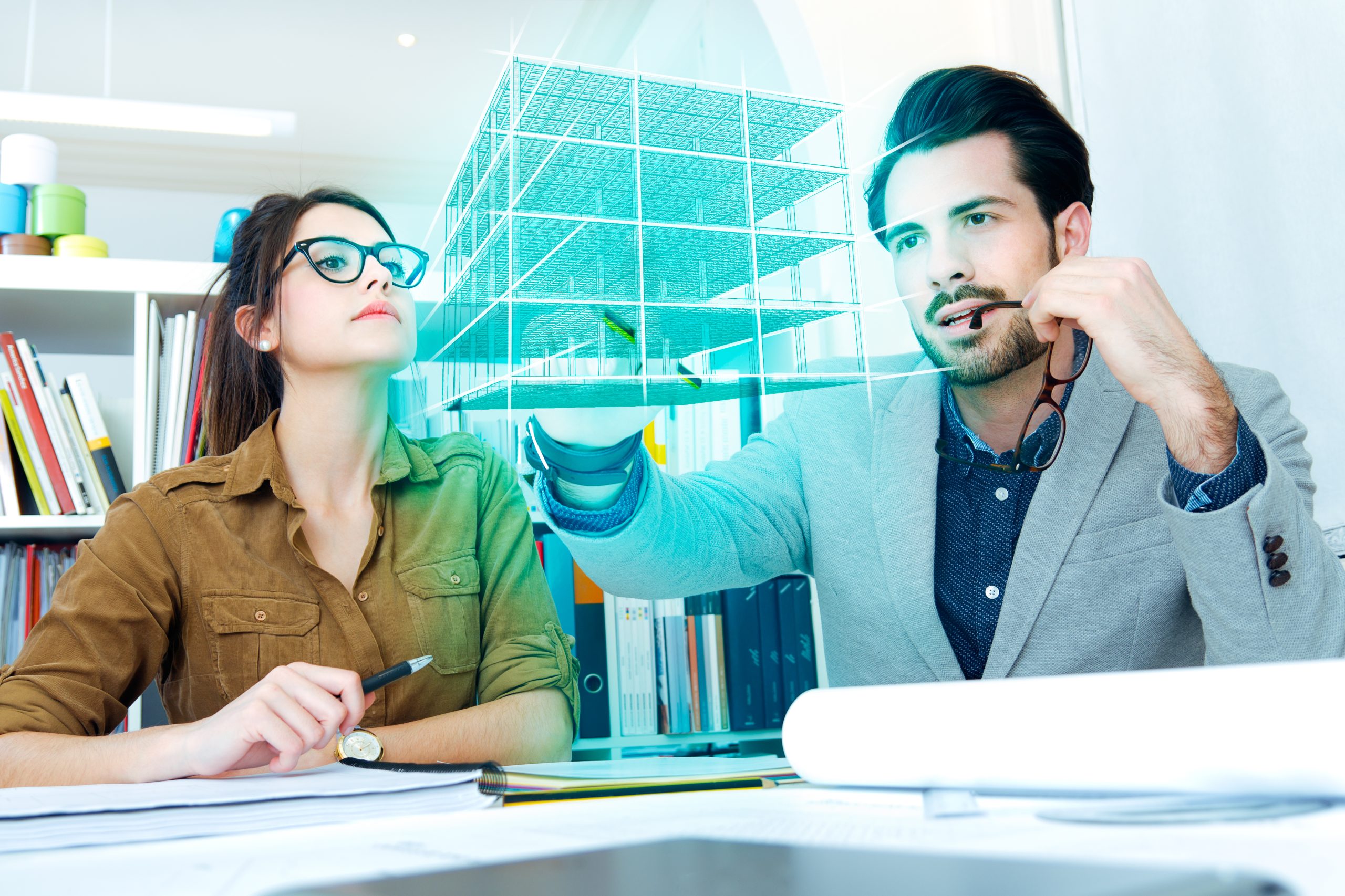
Digital Twins Revolutionize Workforce Training for Skill Growth
Digital twin technology is changing the way employees learn. It provides virtual replicas of real-world systems. This helps workers practice tasks in a safe, realistic environment. In this post, you will discover how digital twins transform skill development.
What Are Digital Twins and Why Do They Matter?
Digital twins are virtual models of physical objects or processes. They mirror real systems in real time. Sensors collect data from physical assets. Then, digital twin software updates the virtual replica with live information.
These replicas help employees understand equipment without direct physical contact. Workers can explore different scenarios and see how systems respond. This promotes faster skill development in a controlled setting. Employees improve their capabilities without risking damage or downtimes.
Key Benefits of Digital Twins
-
Realistic Training Environments
Digital twin solutions offer true-to-life scenarios. Employees face challenges they might see in real-world operations. This fosters better decision-making and problem-solving skills. -
Safer Practice Sessions
Safety is a major concern in workforce training. Digital twin simulations allow employees to make mistakes and learn from them. There is no risk of harming equipment or co-workers. -
Cost Savings
Physical training can be expensive. Equipment, materials, and travel costs add up. By using digital twins, companies cut these costs and still deliver quality training. -
Scalable and Repeatable
Digital twins offer consistent training sessions. Every employee can receive the same standard of instruction. This is especially helpful for large organizations with many global sites.
How Digital Twins Enhance Workforce Training
Digital twins offer immersive learning experiences. They go beyond typical classroom lectures. Instead, employees gain hands-on practice in a virtual space.
1. Interactive Simulations
Trainees see each step of a process in a digital model. They can adjust parameters and observe results. This helps them understand cause-and-effect relationships. It also accelerates skill development when dealing with complex systems.
2. Personalized Feedback
Digital twin platforms track each action a trainee takes. They log performance data and show areas to improve. This feedback loop is immediate and precise. It encourages employees to refine their methods.
3. Safe Failure and Recovery
Mistakes are part of learning. In a digital twin environment, employees can fail without real-world costs. Then, they can retry until they master the skill. This cycle of trial and error builds confidence and competence.
Skill Development Through Digital Twin Technology
Digital twins can shorten the learning curve for new hires. They also help seasoned employees upgrade their knowledge. Here are some ways digital twin technology drives skill development.
Accelerated Onboarding
Newcomers often learn best through hands-on experience. However, giving them direct access to critical assets can be risky. Digital twins solve this by simulating processes. This helps new hires gain competence faster.
Advanced Troubleshooting
Troubleshooting in a digital world removes guesswork. Employees can test multiple solutions in a short time. Once they pick the right approach, they can apply it on the physical system. This fine-tunes problem-solving skills in real situations.
Continuous Learning
Digital twins support ongoing training. As technology evolves, digital replicas can be updated. Employees stay current on new methods and tools. This keeps the workforce agile and competitive.
Applications of Digital Twins in Different Industries
Digital twin technology applies to many fields. Below are some industries that see big gains in workforce training and skill development.
Manufacturing
Manufacturers often use complex machinery. Training on these systems can be expensive and risky. With digital twins, employees practice assembly, maintenance, and quality checks. This reduces downtime and boosts overall efficiency.
Healthcare
Healthcare professionals need precise skills. Mistakes in real-life operations can be costly or dangerous. Digital twins let doctors and nurses rehearse procedures. They can practice surgeries and learn how to handle medical devices.
Energy and Utilities
Power plants, wind farms, and electrical grids are complex. Digital twin technology helps staff learn to operate equipment safely. They can also run emergency drills. This keeps employees ready for unexpected issues.
Aerospace and Aviation
Pilots and engineers benefit from virtual flight simulations. They improve their reaction times and learn how to handle malfunctions. Digital twins even replicate entire aircraft systems for deep maintenance training.
Best Practices for Implementing Digital Twins in Employee Training
Implementing digital twins requires planning. Below are steps to get the most from this technology.
1. Identify Training Goals
Set clear objectives. Do you want faster onboarding, improved safety, or advanced troubleshooting? Defining goals helps you design effective digital twin programs.
2. Collaborate with Experts
Work with software developers and industry specialists. They know how to build accurate simulations. They will also help integrate data from sensors into the virtual models.
3. Test and Refine
Evaluate the digital twin training with a small group first. Gather feedback, measure performance, and make adjustments. This ensures a smooth rollout to the entire workforce.
4. Update Regularly
Real-world systems change over time. Make sure your digital twin is always current. Update it when new equipment is added or processes evolve.
Overcoming Challenges in Digital Twin Adoption
Digital twin technology can face obstacles. Understanding these challenges helps you address them early.
-
High Initial Investment
Software licenses and hardware setups can be costly. However, long-term savings often outweigh these upfront expenses. -
Data Management Issues
Digital twins rely on real-time data. Companies must handle large volumes of information. Implementing secure and scalable data storage is crucial. -
Skill Gap for Implementation
Teams need specialized knowledge. This includes software engineering and data analytics. Offering in-house training or hiring experts helps fill the gap.
Measuring Success in Digital Twin Training Programs
It is vital to track the impact of digital twin programs. Use clear metrics that align with your goals.
- Completion Rates: How many employees finish their digital training modules?
- Performance Metrics: Do employees perform tasks faster or more accurately after training?
- Reduced Downtime: Has equipment downtime decreased because of better-trained staff?
- User Feedback: Collect feedback to improve the training experience.
Collecting these metrics will show whether your digital twin investment is paying off. It will also point to areas for future development.
Conclusion
Digital twins are transforming workforce training and skill development. They create realistic training environments that reduce risk and costs. Through virtual simulations, employees learn faster, practice safely, and gain confidence. Many industries, from manufacturing to healthcare, already see the benefits.
As technology evolves, digital twin solutions will become more accessible. Companies that embrace this shift will likely have a skilled, agile workforce. Now is the time to explore digital twins for your employee training needs. By doing so, you can stay competitive and drive business growth.
Frequently Asked Questions
Q1: What is a digital twin in the context of workforce training?
A digital twin is a virtual representation of physical systems. In workforce training, it helps employees practice tasks without handling real equipment.
Q2: How do digital twins improve skill development?
They offer realistic, hands-on practice. Workers learn complex tasks in a safe environment and get immediate feedback.
Q3: Which industries benefit most from digital twin technology?
Many sectors benefit, including manufacturing, healthcare, energy, and aerospace. Any industry with complex systems can gain from digital twins.
Q4: Is it expensive to implement digital twin software?
The initial costs can be high. However, most companies see long-term savings from reduced downtime and streamlined training.
Q5: Can digital twins replace traditional training methods?
They often enhance traditional methods rather than replace them. Combining digital simulations with in-person coaching can yield the best results.
Author Profile
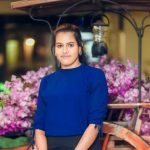
- Online Media & PR Strategist
- Hello there! I'm Online Media & PR Strategist at NeticSpace | Passionate Journalist, Blogger, and SEO Specialist
Latest entries
HPC and AIApril 30, 2025AI and HPC in Gaming: Realistic Virtual Worlds Today
Robotics SimulationApril 30, 2025How Robotics Simulation Agriculture Is Changing Farming
VirtualizationApril 30, 2025Future-Proof Virtualization Strategy for Emerging Tech
Simulation and ModelingApril 30, 2025Chaos Engineering: Build Resilient Systems with Chaos Monkey