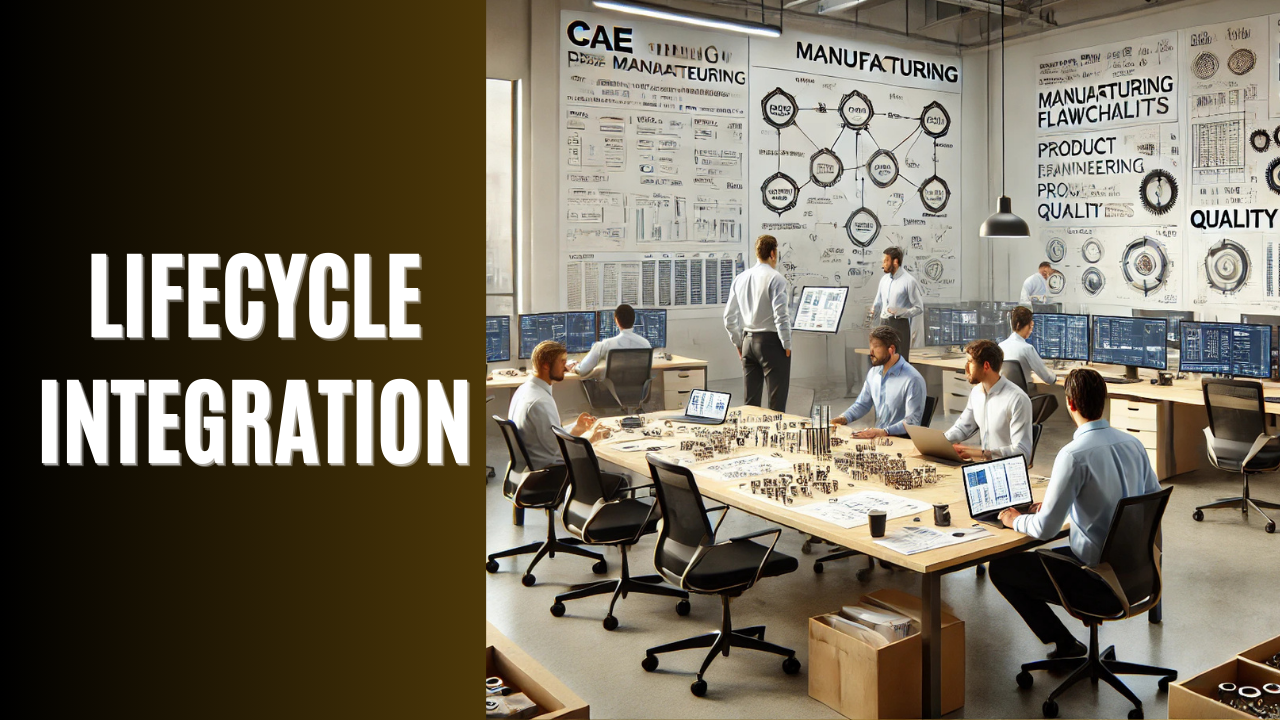
Lifecycle Integration: Connecting CAE Results With Broader Product Development Stages
Have you ever finished a design, only to find major issues during manufacturing? That’s where lifecycle integration comes in. It connects Computer-Aided Engineering (CAE) results with every step of product development—from concept to quality assurance. In this article, you’ll learn how integrating CAE data with manufacturing and quality processes leads to stronger products and efficient workflows.
Lifecycle integration is not just a buzzword. It’s a real way to link teams, reduce redesigns, and improve product performance. By sharing CAE insights across departments, you minimize wasted effort and ensure a smoother launch. Keep reading to see how you can apply this approach in your organization.
What Is Lifecycle Integration?
Lifecycle integration means passing data and insights between all stages of a product’s life. It starts early, during concept design, and continues through engineering, production, and into service. CAE results often inform design choices. These same results can guide process decisions in manufacturing and inform checks in quality assurance.
The goal is to avoid silos. Too often, teams work in isolation. Engineers run simulations, but they may not share details with manufacturing or quality. This disconnection leads to errors and last-minute design changes. With lifecycle integration, everyone taps into the same source of truth.
Why Lifecycle Integration Matters
First, it reduces costs. Late-stage design changes can be expensive. If you find issues after the product is on the assembly line, you pay for retooling or wasted materials. By integrating CAE data, potential problems appear earlier.
Next, it speeds up development. When teams share data, they don’t need to wait for feedback loops or re-run the same calculations. This shortens the product launch timeline.
Finally, it improves product quality. If the CAE team knows manufacturing limits, they can tailor designs to real-world production conditions. Quality teams can also set realistic checks based on predicted stress or fatigue data. This synergy ensures a better final product.
The Role of CAE in Product Development
CAE allows engineers to predict how a product behaves under loads, temperature changes, or motion. Typical analyses include:
- Finite Element Analysis (FEA): Evaluates stress, deformation, or thermal conditions.
- Computational Fluid Dynamics (CFD): Looks at fluid flow around or through a design.
- Multibody Dynamics (MBD): Studies the motion of moving parts under force or gravity.
These simulations yield insights that shape critical decisions. For instance, FEA results may suggest a thinner wall thickness can handle the same load, saving material costs. CFD results may guide changes in geometry to improve airflow or cooling. By linking these results with later stages, you keep the entire process aligned.
Key Stages in the Product Lifecycle
The product lifecycle usually follows these stages:
- Concept and Design
Brainstorming and initial layouts. Designers sketch ideas and gather requirements. - Engineering and Analysis
Detailed models and CAE simulations. Engineers refine geometry and validate performance. - Manufacturing Planning
Determining factory processes, tooling, and materials. Checking feasibility and cost. - Production
Actual fabrication or assembly of the product. - Quality Assurance
Testing and inspections to ensure the product meets specs. - Maintenance and Support
After launch, you track performance, warranty claims, or potential improvements.
Lifecycle integration aims to keep data flowing across these phases. What you learn in one stage informs decisions in the next.
Linking CAE Results to Manufacturing
CAE can reveal the best shape or material for a part. But the perfect design on paper may be tough to manufacture. That’s where integration helps. When CAE data merges with manufacturing planning, you balance ideal performance with real-world production limits.
Examples of Integration
- Optimized Wall Thickness
FEA might show you can reduce thickness by 10%. But manufacturing might need consistent thickness for injection molding. You find a middle ground that satisfies both performance and production feasibility. - Thermal Distortion Predictions
A CFD study could warn about heat build-up in a part. Manufacturing can adjust cooling times or tool designs to maintain tolerances. - Material Selection
CAE might show a certain alloy is lighter yet strong enough. Manufacturing teams then assess cost or supply chain constraints. Everyone aligns on a final choice.
Manufacturing teams also feed back data on actual processes. If a part warps during assembly, that info goes to the CAE team. Next time, they tweak the model or run a new simulation with updated assumptions. This loop keeps designs practical and production-friendly.
Integrating CAE With Quality Processes
Quality checks ensure products meet design specs. But how do you decide where to measure, or which tests to run? CAE results can guide these decisions.
- Critical Areas
Stress plots from FEA show high-stress zones. The quality team focuses inspections on those spots, checking for cracks or flaws. - Tolerance Studies
CAE results can predict how part geometry affects performance. Quality can then set more precise tolerance limits. - Fatigue and Durability
If simulations show certain areas will face repeated stress, quality plans fatigue tests for those points. They track early signs of wear or failure.
By linking these teams, you catch quality issues before mass production. You also gather real data from inspections, which can inform future simulations. This ongoing cycle improves accuracy and reduces product returns or warranty claims.
Tools That Support Lifecycle Integration
Several platforms and software options help merge CAE data with manufacturing and quality data. Here are some popular choices:
- Product Lifecycle Management (PLM) Systems
Tools like Siemens Teamcenter or PTC Windchill store design files, simulation results, and manufacturing plans in one place. - Enterprise Resource Planning (ERP)
Systems like SAP or Oracle can integrate project timelines, resource costs, and inventory tracking. - Manufacturing Execution Systems (MES)
Track production data. These systems can link with CAE-based process plans. - Quality Management Systems (QMS)
Tools like MasterControl or Arena QMS log inspection reports and test data, aligning them with CAE predictions.
When these tools share databases or APIs, teams can access consistent info. This fosters collaboration and real-time insights.
Real-World Applications
Lifecycle integration is found across many industries. Below are some examples:
- Automotive
Engineers run crash simulations to meet safety standards. Manufacturing uses the results to design stronger welds or rivets in critical areas. Quality then tests these joints during production to confirm reliability. - Aerospace
Stress and vibration analyses guide the design of aircraft components. Factories adapt tooling for complex geometries. Quality teams run non-destructive tests on areas flagged by CAE as high-stress zones. - Consumer Electronics
Heat simulations reveal hot spots in circuit boards. Manufacturing adjusts cooling fans or heat sinks. Quality checks those components to ensure proper airflow and thermal performance. - Medical Devices
Simulation results show how implants behave under load. Manufacturing uses that data to refine CNC machining or additive printing. Quality then tests mechanical properties to meet health regulations.
Each case highlights how data flows from CAE to every step, improving the final product.
Overcoming Common Challenges
Lifecycle integration isn’t always easy. It can face hurdles such as:
- Data Silos
Different teams use separate systems or file formats. You need a unifying platform or solid data-exchange process. - Cultural Resistance
Some groups may be set in their ways or fear the extra work. Leadership must emphasize the shared benefits and provide training. - Complex Processes
Large organizations have multiple product lines and legacy systems. A phased approach to integration often works better than an all-at-once push. - Cost and ROI
New software or consulting fees can be high. Identify a pilot project to prove the value before wider rollout.
Addressing these issues early helps ensure a smooth path to full lifecycle integration.
Future Trends in Lifecycle Integration
Technology evolves rapidly. Some emerging trends include:
- Digital Twins
Real-time models of products in operation. These can update based on sensor data and feed back into CAE predictions. - AI-Driven Insights
Machine learning can spot patterns or predict manufacturing issues from simulation data. This speeds up root-cause analysis. - Cloud Collaboration
More teams use remote platforms to share simulation and manufacturing data. This boosts collaboration, especially for global workforces. - Augmented and Virtual Reality
Engineers can visualize CAE results in a 3D space. Manufacturing or quality staff can use these tools to see potential problems before production starts.
These advances make integration faster, more accurate, and easier to scale. But they also require careful planning and secure data management.
Step-by-Step Tips for Successful Integration
Below is a simple checklist to guide your team:
- Define Objectives
Identify the specific goals for integrating CAE with later stages. - Map the Data Flow
Clarify how simulation results move from engineering to manufacturing and quality. - Choose the Right Tools
Investigate PLM, QMS, or MES solutions that can share data seamlessly. - Train Teams
Offer training so everyone understands how to read and use CAE outputs. - Start Small
Test lifecycle integration on a single project. Gather feedback and refine your approach. - Measure Success
Track changes in defect rates, rework costs, and time-to-market.
Following these tips helps you realize the benefits of lifecycle integration without overwhelming your organization.
Conclusion
Integrating CAE results with broader product development stages is a game-changer. It breaks down silos, saves time, and boosts product quality. First, align teams around the common goal of sharing data. Next, pick the right tools to enable a steady flow of information. Finally, monitor and refine the process as you learn from real-world feedback.
This approach benefits every phase, from concept to quality checks. By connecting simulations to manufacturing, you design parts that are simpler to produce and less likely to fail. Quality teams catch issues early, guided by stress or flow data from CAE. The result is a better product with fewer late-stage surprises.
If you’ve struggled with product delays or costly rework, lifecycle integration might be your missing link. Embrace it, and you’ll see how a connected process raises your team’s productivity and your product’s reliability. Stay informed about new tools, and keep refining your methods. Over time, you’ll master a smooth, efficient, and unified product lifecycle.
Author Profile
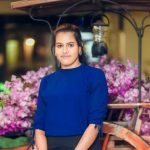
- Online Media & PR Strategist
- Hello there! I'm Online Media & PR Strategist at NeticSpace | Passionate Journalist, Blogger, and SEO Specialist
Latest entries
HPC and AIApril 30, 2025AI and HPC in Gaming: Realistic Virtual Worlds Today
Robotics SimulationApril 30, 2025How Robotics Simulation Agriculture Is Changing Farming
VirtualizationApril 30, 2025Future-Proof Virtualization Strategy for Emerging Tech
Simulation and ModelingApril 30, 2025Chaos Engineering: Build Resilient Systems with Chaos Monkey