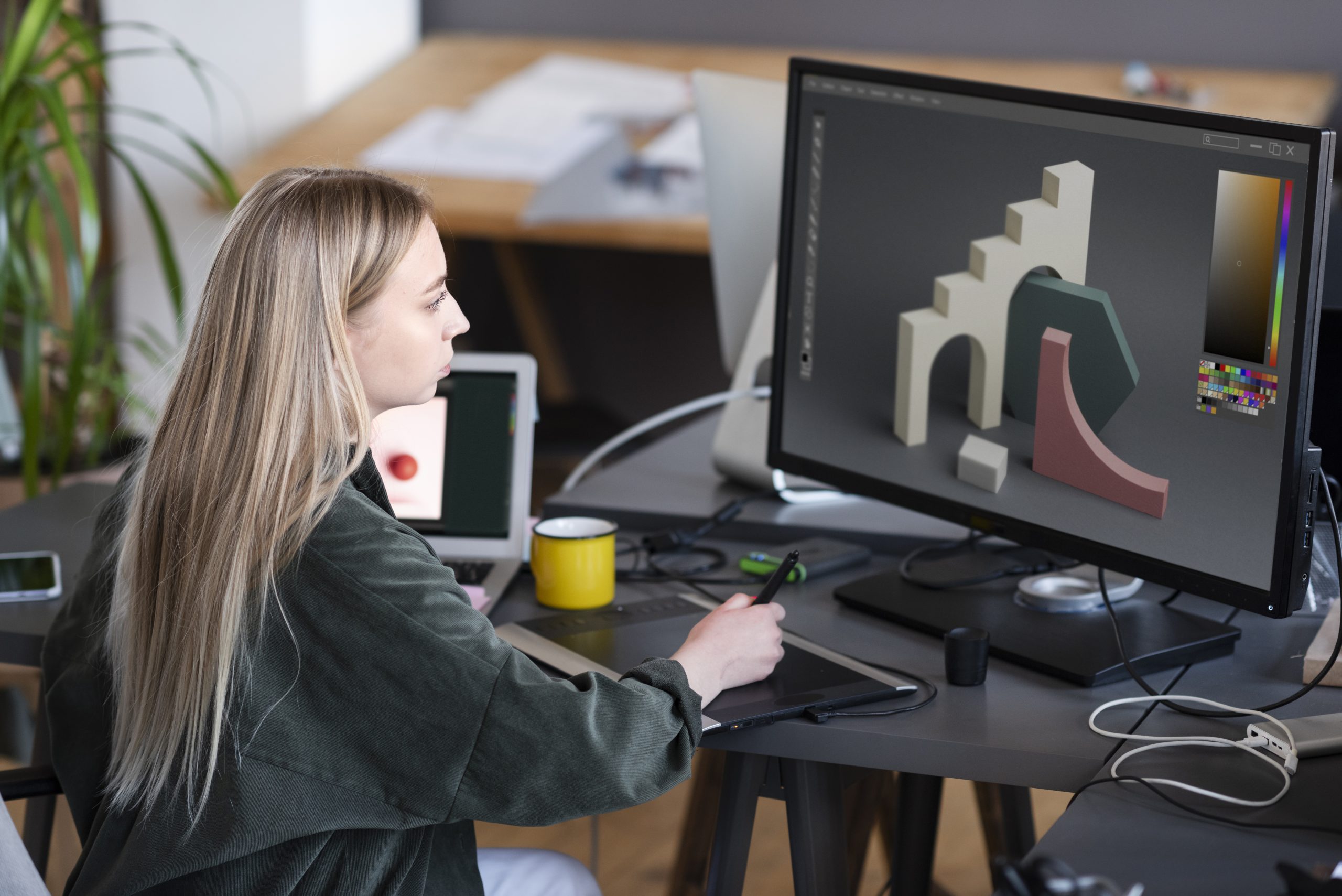
Creation of Detailed Digital Models of Parts and Assemblies
Introduction
Are you curious about how engineers create complex products with perfect fits? In this post, you’ll learn how detailed digital models of parts and assemblies come to life. We’ll explore the software, steps, and best practices that guide this exciting design process. By the end, you’ll understand how to build accurate 3D models and share your design intent with your team.
What Are Digital Models of Parts and Assemblies?
Digital models are 3D representations of real-world parts. They show precise geometry, dimensions, and material properties. These models help engineers visualize, test, and refine their designs before production. Digital models can represent a single part or a complete assembly with multiple interconnected components.
Importance of Detailed Digital Models
Detailed models matter because they reduce design errors. They also ease communication among engineers, clients, and manufacturers. Models help you find issues early, like collisions between parts or poor tolerances. Catching problems sooner saves time and money in the long run.
Types of Digital Models
Engineers often separate models into two main types: part models and assembly models. Part models focus on individual components like gears or brackets. Assembly models bring those parts together in a single structure. Both types are vital to modern engineering and manufacturing.
Benefits of Creating Detailed Digital Models
Digital modeling has many advantages. First, it boosts visualization. You can rotate and zoom in on every angle of a component. Second, it makes detecting interferences between parts easier. Finally, it streamlines the product development cycle by enabling quick design changes.
Improved Visualization and Communication
A 3D model shows shape, dimensions, and fit. This clarity helps team members speak the same language. It eliminates confusion caused by abstract 2D drawings. Plus, it’s easier to explain design choices when others can see the model on a screen.
Interference Detection and Analysis
When multiple parts come together, they can clash or interfere if not designed properly. Detailed models allow quick collision checks. This prevents costly fixes later in the manufacturing process. It also improves overall product quality and ensures all parts fit together well.
Facilitation of Design Changes and Collaboration
Teams often need to revise designs. With digital models, you can modify one feature and instantly see how it affects the rest. This ability makes it faster to adjust shapes, dimensions, or materials. It also promotes collaboration across different departments.
Streamlined Product Development Process
A well-defined 3D model shortens the path to market. It helps identify issues early, while changes are cheap. You can then finalize production plans with greater confidence. That means fewer surprises during the assembly stage and a smoother rollout overall.
Part Modeling
Part modeling is the foundation of building complex products. Each component needs accurate geometry and materials. These steps ensure your part stands on its own and fits with others.
Software and Tools for Part Modeling
Many CAD (Computer-Aided Design) programs support part modeling. Popular choices include SOLIDWORKS, Autodesk Inventor, Creo, and CATIA. Each software offers tools for 2D sketches and 3D features. Look for robust constraint systems, parametric features, and user-friendly interfaces.
Steps in Creating a Detailed Part Model
- Define Requirements: Start with specs and design goals. Ask questions like: how strong must it be? What are the size limits?
- Sketching in 2D: Build a basic outline. Add lines, arcs, and circles.
- Create 3D Features: Extrude or revolve the 2D sketch. Use sweeps or lofts if needed.
- Apply Constraints and Dimensions: Lock down geometry to ensure accuracy.
- Add Details: Include fillets, chamfers, or holes. Patterns can reduce time if features repeat.
- Technical Drawings: Generate 2D drawings with views, dimensions, and notes for manufacturing.
These steps form a repeatable process for any part. They allow you to refine geometry until it meets form, fit, and function.
Assembly Modeling
Assembly modeling is about combining parts into a coherent system. This process shows how pieces fit together and behave under stress or motion.
Techniques for Assembly Modeling
There are two major approaches: top-down design and bottom-up design. Both have benefits, and choosing the right one depends on your project goals.
Top-Down Design
In top-down design, you start with the main assembly. Then you create individual parts inside that assembly. This method keeps everything tied to the overall design intent.
- Efficiency: Changes at the assembly level instantly update all parts.
- Design Intent: It’s easier to see how each component affects the final product.
- Tool Highlight: Some software, like Creo’s Advanced Assembly Extension (AAX), makes top-down modeling easier.
Bottom-Up Design
In bottom-up design, you build parts first. Then you gather them into an assembly. This method often suits teams that want to develop parts in parallel.
- Parallel Development: Different engineers can design separate parts at the same time.
- Reusability: You can reuse parts or subassemblies in future projects.
- Tool Highlight: Add-ons like Intelligent Fastener Extension (IFX) can detect interferences and manage assembly details.
Best Practices for Assembly Modeling
A strong assembly model follows certain rules. First, use clear naming conventions. This avoids confusion when dealing with multiple files. Next, apply constraints or mates properly so parts fit exactly as intended. Finally, create simplified representations for large assemblies to keep system performance high.
- Naming Convention: Label parts logically, like “Gear_01” or “Shaft_Main.”
- Constraints and Mates: Align edges and faces accurately.
- Simplified Representations: Reduce details for performance gains.
- Large Assembly Management: Split big designs into subassemblies when possible.
By following these guidelines, you’ll handle complex projects with ease.
Concurrent Engineering and Collaboration
Concurrent engineering helps teams design products faster. It allows multiple people to work on different aspects at once without waiting for final designs.
The Role of Concurrent Engineering
Concurrent engineering is a workflow. It organizes the design process so tasks overlap rather than occur in sequence. System engineers often set the main design intent. Then sub-teams dive into creating parts and subassemblies. This speeds up the process and encourages better communication.
- Increased Collaboration: Teams share data in real time.
- Reduced Costs: Problems get caught sooner, lowering rework expenses.
- Improved Quality: Designs are refined continuously with input from various experts.
Collaboration Tools and Techniques
Digital modeling often happens in the cloud now. Cloud-based CAD lets everyone see changes instantly. Data management systems (PLM) track versions, permissions, and updates. Communication software like Slack or Microsoft Teams helps coordinate tasks and assign responsibilities.
- Cloud-Based CAD: Share design updates instantly.
- PLM (Product Lifecycle Management): Manage file revisions and project scope.
- Project Management Tools: Track deadlines and tasks for the entire team.
Design Intent Control and Visualization
Controlling design intent ensures the final product meets your vision. It guides how each part interacts with the whole assembly.
Communicating Design Intent
Engineers must clearly state the function of every part. Digital models let you embed notes and dimensions. This clarity prevents misunderstandings about why certain features exist. Top-down assembly design further highlights how each part relates to system requirements.
Visualizing Dependencies
It’s crucial to see how changes in one part affect others. Many CAD tools offer dependency graphs or parent-child views. When you change a dimension in the main assembly, you can observe how sub-parts adapt. This transparency helps prevent costly redesigns.
Ensuring Manufacturability and Assembly
Once your model is ready, it’s time to ensure it can be manufactured efficiently. Design for Manufacturing (DfM) and Design for Assembly (DfA) are key concepts here.
Design for Manufacturing (DfM) Considerations
- Material Selection: Choose materials that match manufacturing processes.
- Tolerances: Define acceptable variation in dimensions to match production limits.
- Surface Finish: Decide how smooth surfaces must be.
- Process Constraints: Account for how parts are formed, such as injection molding or CNC machining.
Design for Assembly (DfA) Considerations
- Minimize Parts: Fewer parts mean simpler and faster assembly.
- Ease of Handling: Parts should be easy to grip or position.
- Use Standard Components: Screws, nuts, or bolts that are commonly available reduce complexity.
- Clear Instructions: Provide step-by-step assembly directions to guide production teams.
Conclusion
Detailed digital models of parts and assemblies power modern product development. They help you visualize, refine, and validate designs quickly. By using proper CAD tools, following structured workflows, and adopting concurrent engineering, your team can work faster and produce better products. Remember to keep design intent clear, manage assembly constraints carefully, and follow DfM and DfA guidelines.
If you’re ready to elevate your design process, explore more resources or connect with our team. Let digital models guide you toward innovative and efficient solutions. With the right mindset and software, you can transform your ideas into reality.
FAQ
Below are some common questions people ask about creating detailed digital models of parts and assemblies.
What Are Some Common Challenges in Creating Detailed Digital Models?
- Large Assembly Performance: Handling many parts can slow down your system. Use simplified representations.
- Interference Detection: Overlapping geometries can be missed if not checked thoroughly.
- Collaboration Hurdles: Large file sizes can be tough to share. Cloud solutions help ease this issue.
How Can I Ensure the Accuracy of My Digital Models?
Accuracy starts with proper measurements. Double-check dimensions and constraints. Simulation tools let you test loading conditions or motion. This analysis tells you if the design holds up under stress or if it needs tweaks.
What Are the Future Trends in Digital Modeling for Parts and Assemblies?
Additive manufacturing (AM) is changing how parts are designed. Complex shapes that were once impossible are now feasible. Machine learning is also helping automate some tasks, like optimizing part geometry for weight or strength. Finally, sustainability is becoming vital, so more engineers aim to design with eco-friendly materials and processes.
Author Profile
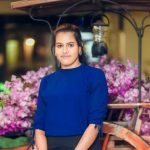
- Online Media & PR Strategist
- Hello there! I'm Online Media & PR Strategist at NeticSpace | Passionate Journalist, Blogger, and SEO Specialist
Latest entries
Artificial InteligenceApril 30, 2025Master Prompt Engineering Techniques for Better AI Output
HPC and AIApril 30, 2025AI and HPC in Gaming: Realistic Virtual Worlds Today
Robotics SimulationApril 30, 2025How Robotics Simulation Agriculture Is Changing Farming
VirtualizationApril 30, 2025Future-Proof Virtualization Strategy for Emerging Tech