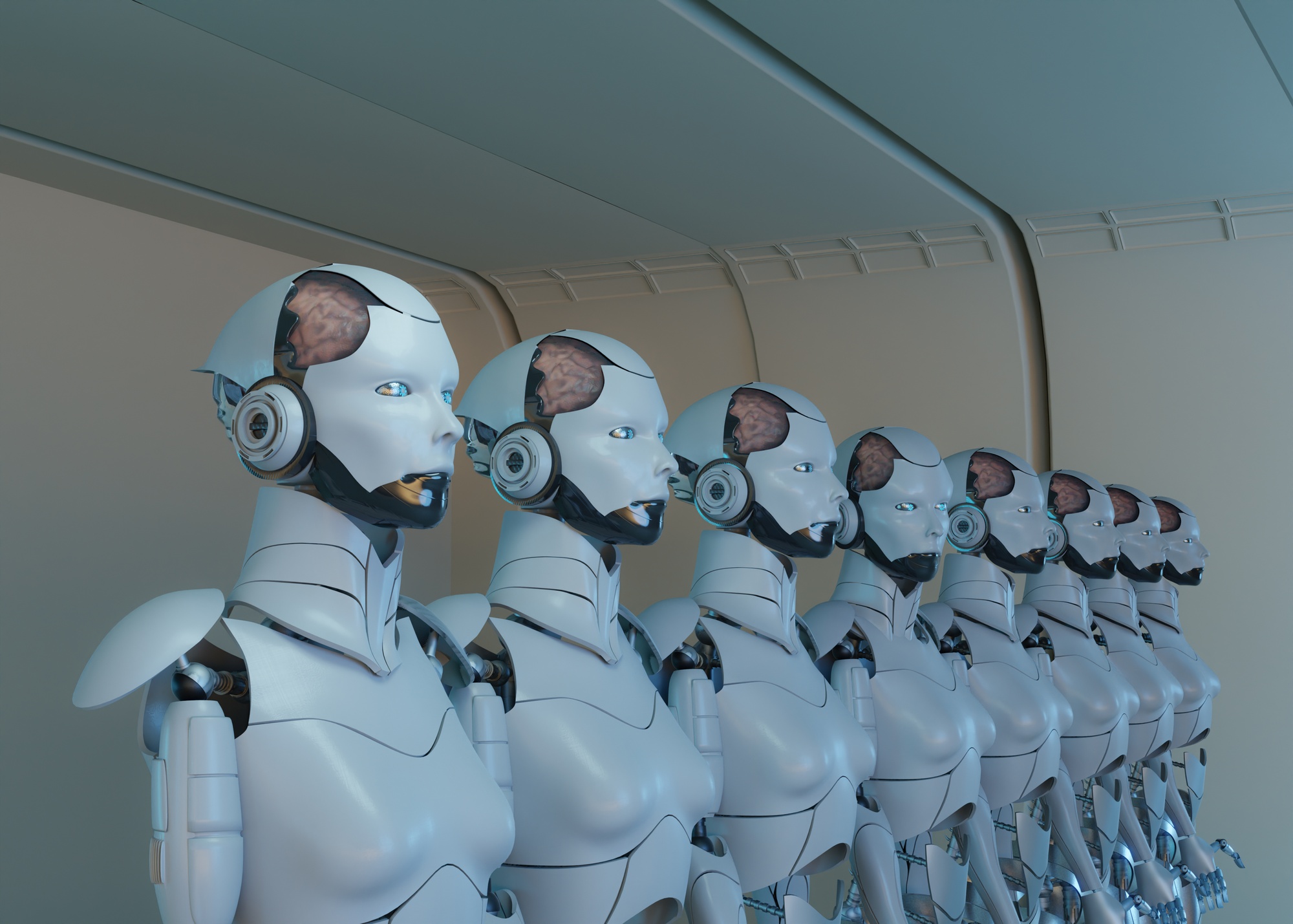
Simulating robots in exoskeleton development
Robotics simulation in developing exoskeletons is transforming lives by aiding recovery and enhancing human abilities. But how do engineers ensure these complex wearable robotic devices function effectively and safely? The answer lies in robotics simulation, a crucial step in designing and testing wearable robotic systems for both medical and industrial applications. In this article, you’ll discover how robotics simulation shapes exoskeleton development and why it matters for real-world use.
Understanding Robotics Simulation and Exoskeletons
What is Robotics Simulation?
Robotics simulation is a digital method to create and test robotic devices in a virtual environment. It allows engineers to model how robots interact with real-world conditions without physical prototypes. This saves significant time, reduces costs, and improves design quality.
Learn more about robotics and automation.
Why Exoskeletons?
Exoskeletons are wearable robotic systems designed to support or enhance human movement. They have significant applications, including:
- Assisting patients with mobility disorders.
- Enhancing worker strength and safety in industrial settings.
- Reducing fatigue and preventing workplace injuries.
Explore our guide to industrial robotics.
How Robotics Simulation Enhances Exoskeleton Development
First: Faster and More Efficient Exoskeleton Design
Simulation speeds up the design phase significantly. Engineers can quickly test multiple exoskeleton configurations virtually. Issues such as mechanical limitations or ergonomic problems can be identified and corrected early, reducing the need for costly redesigns.
Next: Improved Safety and Reliability in Robotic Exoskeletons
Safety is crucial when humans rely on robotic assistance. Robotics simulation allows developers to test exoskeletons under numerous scenarios, such as:
- Sudden movements or stops.
- Weight-bearing capacities.
- Emergency shutdown procedures.
By simulating these situations, engineers ensure exoskeletons perform reliably, reducing the risk of injury.
Finally: Customization for Enhanced Comfort in Wearable Robotics
Comfort greatly influences user adoption of exoskeleton technology. Simulation helps developers analyze how exoskeletons interact with various body types and movements, ensuring maximum comfort and usability. This leads to better user compliance, particularly important for medical rehabilitation and industrial work settings.
Real-Life Applications of Robotics Simulation in Exoskeletons
Robotics Simulation in Medical Exoskeletons
Robotics simulation is crucial in developing medical exoskeletons designed for rehabilitation. For instance, simulations can accurately mimic patient movements, allowing precise adjustments for comfort and effectiveness in therapy. Exoskeletons such as ReWalk and Ekso Bionics have leveraged simulation for successful deployment in clinical settings.
Robotics Simulation for Industrial Exoskeletons
In industrial environments, exoskeletons help reduce physical strain and enhance productivity. Robotics simulations allow designers to test exoskeleton performance during heavy lifting, repetitive motions, and extended usage periods. Companies like Sarcos Robotics use simulation extensively to optimize their industrial exoskeleton models.
Challenges in Robotics Simulation for Exoskeletons
Realistic Human Movement Simulation
One significant challenge is accurately simulating realistic human movements. Human motion is complex and varies greatly between individuals. Improving the accuracy of these simulations remains an ongoing focus.
Hardware Integration Challenges
Translating successful simulations into physical prototypes presents another challenge. While simulations provide detailed data, real-world testing remains necessary to refine performance and ensure reliability under diverse conditions.
The Future of Robotics Simulation and Exoskeleton Technology
Advancements in simulation software and increased computational power will continue to boost exoskeleton innovation. Future simulations will provide even more accurate predictions, allowing highly sophisticated, personalized exoskeletons tailored for individual needs.
Emerging Trends in Robotics Simulation:
- Integration of AI to predict optimal design changes.
- Virtual reality (VR) for immersive user experience testing.
- Advanced biometric data collection for more precise simulations.
Frequently Asked Questions (FAQ)
What is robotics simulation?
Robotics simulation uses computer software to virtually design, test, and refine robotic systems without physical prototypes.
Why are exoskeletons important?
Exoskeletons improve quality of life for people with mobility challenges and enhance worker safety and productivity in industrial settings.
How does simulation improve exoskeleton safety?
Simulation allows engineers to test exoskeleton designs in various scenarios, ensuring safety measures are effective before real-world use.
Are simulated exoskeleton tests accurate?
Modern simulation software is highly accurate, but real-world testing is essential to confirm simulation results and fine-tune the final design.
What is the future of robotics simulation for exoskeletons?
The future includes AI-driven predictive simulations, VR-enhanced user experience testing, and more accurate biometric data integration.
Conclusion
Robotics simulation is indispensable for developing advanced exoskeletons, significantly improving their safety, efficiency, and comfort. By leveraging this technology, engineers can rapidly innovate, bringing better exoskeleton solutions to medical and industrial users faster and more reliably.
Author Profile
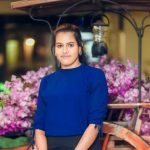
- Online Media & PR Strategist
- Hello there! I'm Online Media & PR Strategist at NeticSpace | Passionate Journalist, Blogger, and SEO Specialist
Latest entries
Robotics SimulationApril 30, 2025How Robotics Simulation Agriculture Is Changing Farming
VirtualizationApril 30, 2025Future-Proof Virtualization Strategy for Emerging Tech
Simulation and ModelingApril 30, 2025Chaos Engineering: Build Resilient Systems with Chaos Monkey
Digital Twin DevelopmentApril 30, 2025How to Ensure Data Synchronization Twins Effectively