
Thermal Analysis: Evaluating Heat Transfer and Thermal Stresses
Have you ever noticed how your phone warms up during heavy use? That’s heat transfer in action. When products heat up, materials expand and can fail over time. This article will teach you how thermal analysis predicts and manages these heat effects.
Thermal analysis focuses on heat transfer and thermal stresses. You will learn what these terms mean, why they matter, and which tools help you model them. By the end, you’ll see how engineers keep devices cool and structures safe in daily use.
Understanding Thermal Analysis
Thermal analysis studies how heat moves and how it causes stress in materials. Heat can flow through conduction, convection, or radiation. Each mode affects your design in a different way.
When a device heats up, parts can expand. If they expand too much, they can warp or crack. Thermal analysis predicts these behaviors so engineers can modify designs before big problems arise.
In many industries, controlling temperature is crucial. Think about cooling a car engine or preventing hot spots in a circuit board. Thermal analysis helps solve these challenges by revealing temperature patterns and stress points.
Why Thermal Analysis Matters
First, it helps you avoid material failure. Overheating can weaken metals, melt plastics, or break adhesives. Predicting thermal stresses keeps products safe and extends their lifespan.
Next, it boosts performance. If a battery or processor overheats, it may slow down or shut off. Good thermal design keeps systems running at their best.
Finally, it saves money. Catching thermal issues early prevents expensive redesigns and recalls. Companies also gain a reputation for reliable products that work under tough conditions.
Types of Heat Transfer
Heat can move in three main ways. Each path affects how we approach thermal analysis.
- Conduction
This is heat flow through solid materials. It depends on the material’s thermal conductivity. Metals, for example, conduct heat better than plastics. - Convection
This is heat transfer via fluids, like air or water. Fans and pumps are used to move the fluid and remove heat. - Radiation
This is heat transfer via electromagnetic waves. The sun warming your face is a good example of radiative heat transfer.
Real devices often involve all three methods. Understanding each helps you build accurate simulations.
Methods and Tools for Thermal Analysis
Thermal analysis can be done in a few ways. Below are some common methods and tools.
1. Analytical Calculations
Engineers can use formulas or simple models to estimate temperature changes. This approach works for simple shapes or quick checks.
2. Numerical Simulation (FEA or CFD)
Software like ANSYS, COMSOL, or Siemens Simcenter uses finite element analysis (FEA) or computational fluid dynamics (CFD). These programs solve complex equations for conduction, convection, and radiation.
3. Physical Testing
Sometimes, you need real data. Engineers use thermal cameras or sensors to measure temperature on prototypes. The results can confirm or refine simulation models.
4. Combined Approaches
Many teams mix simulation and testing. They might build a digital model, run simulations, and compare them to real tests. This loop builds confidence in the final design.
Thermal Stress: A Closer Look
Thermal stress arises when different parts of a material expand by different amounts. If expansion is blocked, stress builds up. This can happen when a material is heated unevenly or when two materials with different expansion rates are joined.
- Uneven Heating
If one side is hot and the other is cool, the expansion will be uneven. This mismatch causes internal forces that can crack the material. - Different Materials
A steel bolt on an aluminum plate can see stress if they heat at different rates. Over time, fatigue cracks can form. - Repetitive Cycles
Products that heat up and cool down repeatedly, like engine parts, face thermal cycling. Stress can build up with each cycle.
Engineers must consider these factors to avoid costly part failures.
Common Steps in Thermal Analysis
Below is a simple outline of how engineers approach a thermal problem:
- Define Geometry and Materials
Create or import a 3D model. Assign each part the correct thermal properties, like conductivity or expansion coefficient. - Set Boundary Conditions
Specify heat sources, ambient temperatures, and fluid flows. Also include any known convection or radiation effects. - Mesh the Model
Break the geometry into small elements or cells for numerical analysis. A finer mesh typically improves accuracy but takes more computation time. - Run Simulation
Use FEA or CFD solvers to calculate temperature distributions and, if needed, thermal stresses. - Analyze Results
Look at temperature gradients and stress hotspots. Check if they exceed safe limits. - Optimize
If certain areas run too hot, add cooling fins or change materials. You might also shift the design to reduce stress concentrations. - Validate with Tests
Build a prototype and measure its temperatures. Compare real data to simulation results.
Following these steps ensures a thorough evaluation of heat flow and thermal stresses.
Industry Applications
Thermal analysis is everywhere. Below are a few fields that rely on it:
- Automotive
Engines, brakes, and electronics all produce heat. Engineers use thermal analysis to avoid overheating and ensure optimal performance. - Aerospace
Aircraft and spacecraft face extreme temperature shifts, from sub-zero conditions to intense engine heat. Thermal modeling is key to safety. - Consumer Electronics
Phones, laptops, and gaming consoles need cooling solutions. Good thermal design prevents damage and improves user comfort. - Power Generation
Turbines, boilers, and solar panels involve high heat flows. Operators want to keep them efficient and safe. - Manufacturing Machinery
Industrial equipment can run for hours or days at elevated temperatures. Predicting heat build-up avoids downtime.
No matter the industry, poor thermal management can lead to breakdowns or safety concerns.
Best Practices and Key Considerations
Thermal analysis is complex, but some guidelines help you avoid mistakes:
- Start with Simple Models
If you’re new to thermal analysis, begin with simple shapes. Get a feel for how heat flows and check your understanding. - Use Accurate Material Data
Properties like thermal conductivity or specific heat matter a lot. Check datasheets or run tests to confirm. - Mind Convection and Radiation
It’s easy to overlook these modes, but they can be big factors in real systems. - Watch for Contact Resistance
Surfaces in contact might not conduct heat perfectly. Gaps or coatings can reduce heat flow. - Incorporate Safety Margins
Conditions in real-world operations can differ from simulations. Add a buffer for unknowns. - Validate Early and Often
Compare simulation results to real measurements. This ensures your model reflects actual behavior.
These tips help you get reliable results and keep your design process on track.
Common Mistakes in Thermal Analysis
Errors can lead to flawed conclusions. Here are a few to watch out for:
- Ignoring Transient Effects
Temperatures can change over time. If you only check steady-state conditions, you may miss surge temperatures or cooldown phases. - Oversimplifying Geometry
Skipping small details can hide local hot spots. If these details matter, refine the model. - Wrong Boundary Conditions
A bad assumption about convection or ambient temperature can throw off your entire result. - Poor Mesh Quality
An overly coarse mesh might not capture steep gradients. Make sure to refine areas of high interest. - Lack of Multiphysics Integration
Heat might cause stress, or fluid flow might drive temperature changes. Separate models might miss these combined effects.
Learning from these mistakes keeps your analysis realistic and avoids rework.
Conclusion
Thermal analysis is vital for evaluating heat transfer and thermal stresses in any design. It helps you foresee hot spots, predict stress buildup, and plan cooling strategies. By mixing simulation and testing, you can save costs, enhance safety, and extend product life.
First, understand heat transfer modes. Next, choose the right tools for your analysis—be it a quick calculation, full FEA model, or real-world experiment. Finally, validate your model with physical tests to ensure accuracy.
Whether you build cars, satellites, or cell phones, controlling temperature is key. Good thermal analysis sets your design apart and keeps it reliable under all conditions. Stay informed, refine your methods, and apply best practices to master thermal challenges.
Author Profile
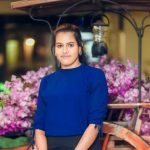
- Online Media & PR Strategist
- Hello there! I'm Online Media & PR Strategist at NeticSpace | Passionate Journalist, Blogger, and SEO Specialist
Latest entries
Data AnalyticsJune 13, 2025Future of Data Warehousing in Big Data
AI InterfaceJune 13, 2025Aligning AI Developments with Corporate Goals in the AI Era
HPC and AIJune 13, 2025HPC Architecture Taking to the Next Level
Quantum ComputingJune 13, 2025Ethical Issues in Quantum Tech: Privacy, Jobs, and Policy