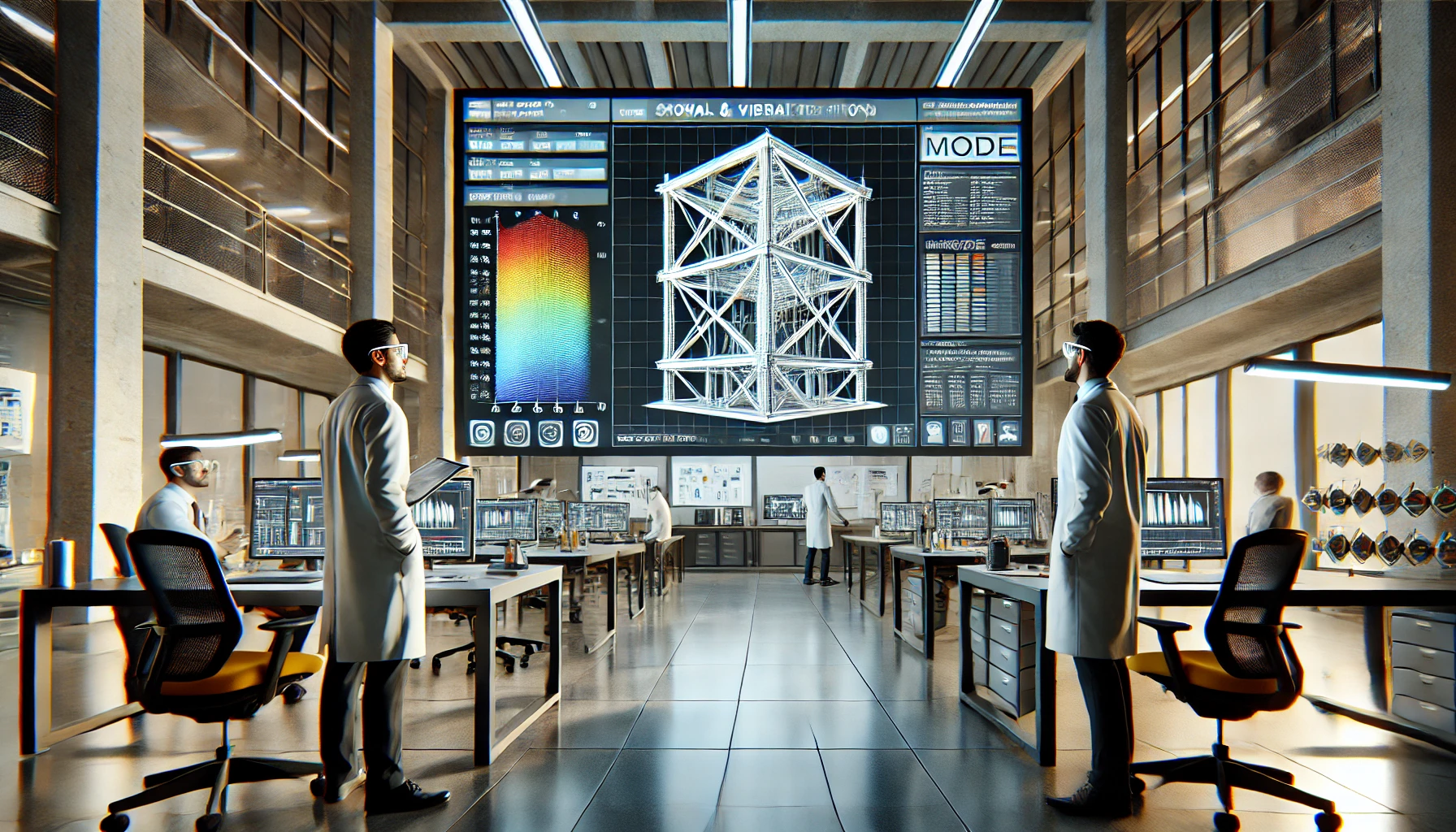
Modal and Vibration Analysis: Studying Natural Frequencies and Dynamic Responses
Have you ever wondered why structures sometimes shake or hum under certain conditions? This happens when they vibrate at their natural frequencies. Understanding this behavior is the core of modal and vibration analysis. In this post, you will learn how engineers study natural frequencies, manage dynamic responses, and create stronger, safer designs.
Vibration analysis is more than a theory. It helps you predict how a structure behaves under real-world forces. From car chassis to skyscrapers, every design needs careful analysis to prevent failure. Keep reading to learn how modal and vibration analysis works and how it ensures structural integrity.
What Is Modal Analysis?
Modal analysis is the study of a system’s natural frequencies and mode shapes. These modes define how a structure vibrates when excited. Each mode has a frequency at which the structure resonates the most.
Engineers often use numerical methods to find these modes. A common method is the Finite Element Analysis (FEA). FEA breaks the structure into elements and computes the vibration characteristics of the model.
When you know the modes, you can predict how the structure behaves under different loads. This allows you to design or modify it to reduce harmful vibrations.
Why Is Vibration Analysis Important?
First, vibration analysis reveals weak spots in a structure. High vibration can damage components over time. Cracks or fatigue often appear when resonance occurs near a design’s operating conditions.
Next, controlling vibrations leads to better performance. Think of a vehicle’s suspension system. Reducing unwanted shaking improves comfort and control.
Finally, vibration analysis can help you save costs. By identifying potential issues early, you avoid expensive fixes later. You also reduce the risk of product recalls or safety failures.
Common Terms in Modal and Vibration Analysis
Understanding key terms makes learning this topic easier. Below are a few essential ones:
- Natural Frequency
The frequency at which a structure vibrates freely. At this frequency, vibrations can amplify if not controlled. - Mode Shape
The pattern a structure follows when vibrating at a specific natural frequency. Different modes can appear at different frequencies. - Resonance
An amplified response that occurs when the excitation frequency matches a structure’s natural frequency. - Damping
Energy dissipation in a vibrating system. Damping reduces vibration amplitude by converting motion into heat or other forms of energy. - Excitation
Any force or input that triggers vibrations in a system. Examples include wind, impacts, or rotating machinery.
Knowing these terms helps you navigate technical details. You will see them often in analysis reports and software.
Steps in Performing Modal and Vibration Analysis
Below is a typical workflow for studying a structure’s dynamic responses:
- Define the Geometry
Start by creating or importing a 3D model. CAD software is often used for this step. - Material Properties
Specify material parameters such as density, Young’s modulus, and Poisson’s ratio. These values affect how the structure vibrates. - Meshing the Model
Use finite element software to split the geometry into small elements. An accurate mesh leads to more reliable results. - Apply Boundary Conditions
Set constraints to mimic real-world supports or connections. For instance, a bolted joint or a fixed end. - Perform Modal Analysis
Let the solver calculate the natural frequencies and mode shapes. This reveals how the structure vibrates in its free or unforced state. - Conduct Harmonic or Transient Analysis
Study how the structure responds under a range of frequencies or time-based loads. Identify resonance peaks or abrupt changes in vibrations. - Interpret Results
Look at displacement plots, stress distributions, or frequency response curves. Check if any modes align with the operating frequency range. - Refine the Design
Adjust thickness, shape, or damping features to shift critical frequencies. The goal is to avoid resonance under normal conditions.
By following these steps, you gain deep insights into the structure’s dynamic behavior. This approach prevents surprises and helps you optimize your design before physical tests.
Techniques and Tools
Different techniques can help you run a thorough modal and vibration analysis. Each serves a unique purpose. Below are some popular methods and tools:
Finite Element Analysis (FEA)
FEA is the backbone of many engineering studies. It uses a numerical approach to solve partial differential equations that govern vibrations. Tools like ANSYS, ABAQUS, or Siemens Simcenter handle complex geometries. They offer built-in solvers for modal, harmonic, and transient analyses.
Experimental Modal Analysis (EMA)
EMA involves physical testing on actual prototypes. Engineers apply known forces to measure the response with sensors such as accelerometers. This helps validate numerical predictions. You also gain real data about damping and system stiffness.
Operational Modal Analysis (OMA)
OMA is performed while the structure is in normal operation. It does not need artificial force inputs. Instead, it measures vibrations from ambient or operational loads. For big structures like bridges or ships, OMA is a practical approach.
Analytical Approaches
Simple structures might allow closed-form equations. For instance, a beam or a plate can be solved with classical formulas. Although less common in complex designs, these formulas are still valuable for quick checks.
Interpreting Results
Data from modal and vibration analysis can be vast. Below are ways to understand what the numbers mean:
- Identify Critical Frequencies
Check which frequencies are near your operating range. If the equipment runs at or near a natural frequency, consider design changes or add damping. - Examine Mode Shapes
See how the structure deforms for each mode. Look for regions with large displacements. These may need reinforcement. - Plot Frequency Response
Frequency response functions (FRFs) show how a system responds across a range of frequencies. Sharp peaks hint at potential resonance. Flatten those peaks to control vibrations. - Evaluate Stresses
Many software tools link vibration analysis to stress calculations. Peak stress often happens near resonance. This data can guide material choices or design tweaks. - Compare With Safety Standards
Match the results with industry guidelines. For example, some standards require safety margins on frequencies or deflections.
Gathering results is not enough. Good interpretation leads you to the right engineering decisions.
Industry Applications
Modal and vibration analysis is useful in many fields. Here are a few examples:
- Automotive
Car frames, engines, and drive systems must avoid harmful vibrations for safety and comfort. Modal analysis ensures key components do not shake at common engine speeds. - Aerospace
Aircraft wings, fuselages, and spacecraft structures face strong dynamic forces. Engineers study their behavior to prevent fatigue and ensure stable flight. - Civil Engineering
Buildings, bridges, and towers endure wind, traffic, and seismic loads. Vibration analysis helps design safer and more durable structures. - Manufacturing Machinery
Rotating parts and production lines often generate vibrations. Controlling these vibrations boosts precision and reduces downtime. - Consumer Electronics
Even small devices like smartphones experience vibration. Modal analysis helps keep them intact and functioning under normal use.
By controlling vibrations, industries save money, reduce downtime, and enhance user safety.
Avoiding Common Mistakes
Mistakes in modal and vibration analysis can lead to flawed results. Watch out for these issues:
- Poor Mesh Quality
A coarse or poorly shaped mesh gives inaccurate frequency results. Refine the mesh in high-strain regions. - Wrong Boundary Conditions
Incorrect supports or loads skew the analysis. Make sure they reflect real-world conditions. - Ignoring Damping Factors
Many designs include some damping. Overlooking it can lead to overestimated resonance peaks. - Focusing on One Mode Only
Structures have multiple modes. Always review the first few modes to avoid missing a critical frequency. - Lack of Validation
If possible, compare FEA results with physical tests. This helps confirm the accuracy of your model.
Avoiding these pitfalls helps you produce reliable simulations that match real-world performance.
Conclusion
Modal and vibration analysis is essential for modern engineering. It reveals how structures vibrate and guides designers to safer, more efficient products. By understanding natural frequencies and managing dynamic responses, you can prevent costly failures.
First, decide on the right approach. A combined numerical and experimental method is often best. Next, apply best practices like refining your mesh and validating boundary conditions. Finally, interpret the data carefully. Look at frequency peaks, mode shapes, and stress levels to ensure a robust design.
Remember, even small changes in a design can shift natural frequencies. These shifts may save your product from damaging vibration. Whether you’re in automotive, aerospace, or civil engineering, mastering modal analysis offers a critical advantage. Embrace this method and keep your structures strong, safe, and reliable.
Author Profile
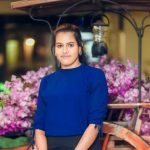
- Online Media & PR Strategist
- Hello there! I'm Online Media & PR Strategist at NeticSpace | Passionate Journalist, Blogger, and SEO Specialist