
Mastering the Thermal Analysis Process for Heat Management
Heat can build up in machines, electronics, and buildings. If it’s not managed, it causes failure or damage. That’s why the thermal analysis process is important.
In this blog, you’ll learn how this method helps engineers understand heat transfer and how materials handle temperature changes. You’ll also find practical uses, tools, and common challenges. Whether you’re an engineer or a student, you’ll gain clear, useful insights.
What Is the Thermal Analysis Process?
The Thermodynamic analysis helps engineers study how materials and systems respond to heat. It includes measuring heat transfer, temperature changes, and thermal stress.
This process helps:
-
Predict how a system behaves under heating or cooling
-
Avoid damage from overheating
-
Improve energy efficiency and safety
These results guide design choices in industries like electronics, aerospace, and manufacturing.
Why the Thermodynamic analysis Matters in Engineering
Systems like smartphones, engines, or bridges heat up during use. If not managed, heat can:
-
Crack materials
-
Weaken structures
-
Shorten lifespan
The thermal analysis process shows:
-
How heat flows through a material (conduction, convection, radiation)
-
Where hot spots form
-
How much stress builds due to expansion or shrinkage
Benefits:
-
Improved design accuracy
-
Early failure detection
-
Reduced downtime and costs
To dive deeper, check out this overview of thermal modeling tools (outbound link).
Steps in the Thermal Analysis Process
The thermal analysis process typically includes:
1. Define the System
-
Choose the material or product
-
Set temperature ranges and load conditions
2. Create a Thermal Model
-
Use CAD or FEA tools
-
Build a 3D representation
3. Apply Heat Sources and Boundaries
-
Add temperature inputs like environmental heat or internal sources
-
Define cooling methods (airflow, water)
4. Simulate Heat Transfer
-
Use software to calculate thermal behavior
-
Check how heat spreads and where stress forms
5. Interpret the Results
-
Analyze temperature maps
-
Measure expansion, stress points, and failure risks
Internal tools like SolidWorks Simulation (outbound link) are popular for this process.
Types of Heat Transfer in the Thermal Analysis Process
Understanding heat transfer is key. The Thermodynamic analysis considers:
Conduction
-
Heat moves through solid materials
-
Example: metal rods heating up
Convection
-
Heat moves through fluids like air or water
-
Example: CPU fans cooling chips
Radiation
-
Heat transfers through electromagnetic waves
-
Example: sun warming a satellite
Each affects performance differently. Knowing them helps engineers choose the right design.
Thermal Stress and Structural Impact
As materials heat or cool, they expand or shrink. Uneven temperature changes create thermal stress. The thermal analysis process helps identify these stresses.
Risks:
-
Cracks or deformation
-
Joint failures
-
Performance loss
Solutions:
-
Select materials with low thermal expansion
-
Use cooling systems
-
Design flexible joints
You can explore a real-world case from NASA’s spacecraft design principles.
Software Tools for the Thermodynamic analysis
Engineers rely on tools to perform the thermal analysis process. Here are top options:
1. ANSYS
-
High-level simulation for heat and stress
-
Includes multiphysics capabilities
2. COMSOL Multiphysics
-
Flexible tool for coupling thermal and mechanical studies
3. Autodesk CFD
-
Focused on airflow and cooling system analysis
Many of these tools offer student versions or trials to help you learn and apply concepts quickly.
Common Challenges in the Thermal Analysis Process
Despite its benefits, the Thermodynamic analysis faces some issues:
1. Complex Geometry
-
Irregular shapes make modeling difficult
2. Material Properties
-
Not all materials have known thermal data
3. Boundary Conditions
-
Estimating heat sources and airflow can be tricky
Solutions include using accurate data sheets and simplifying models without losing detail.
Best Practices in the Thermodynamic analysis
To get accurate results:
-
Use quality mesh in simulations
-
Validate models with lab testing
-
Update boundary conditions regularly
-
Document assumptions clearly
These practices help improve simulation accuracy and build trust in results.
FAQs
What is the main goal of the thermal analysis process?
To understand how systems behave under temperature changes and prevent heat-related failures.
How is thermal stress calculated?
By using simulation software that factors in material expansion and temperature gradients.
Is thermal analysis only for engineers?
No. Architects, HVAC professionals, and students also use it to improve safety and design.
Which industries use the thermal analysis process?
Electronics, aerospace, automotive, and construction all rely on it for heat management.
Mastering the Thermal Analysis Process
The thermal analysis process is vital for designing reliable systems. By understanding heat flow and thermal stress, engineers avoid damage, save energy, and build safer products.
Want to explore simulation tools? Check out our The Role of Big Data in Enhancing CAE Simulations. Learn how you can apply the Thermodynamic analysis in your projects today.
Author Profile
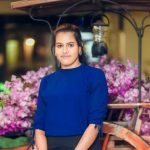
- Online Media & PR Strategist
- Hello there! I'm Online Media & PR Strategist at NeticSpace | Passionate Journalist, Blogger, and SEO Specialist
Latest entries
High Performance ComputingJuly 16, 2025Conversational AI vs. Traditional Chatbots: Pros & Use Cases
Conversational AIJuly 16, 2025How Conversational AI Support Improves Customer Service
Conversational AIJuly 16, 2025How Conversational AI Chatbots Improve Customer Service
Conversational AIJuly 15, 2025How Conversational AI Future is Changing Work Forever