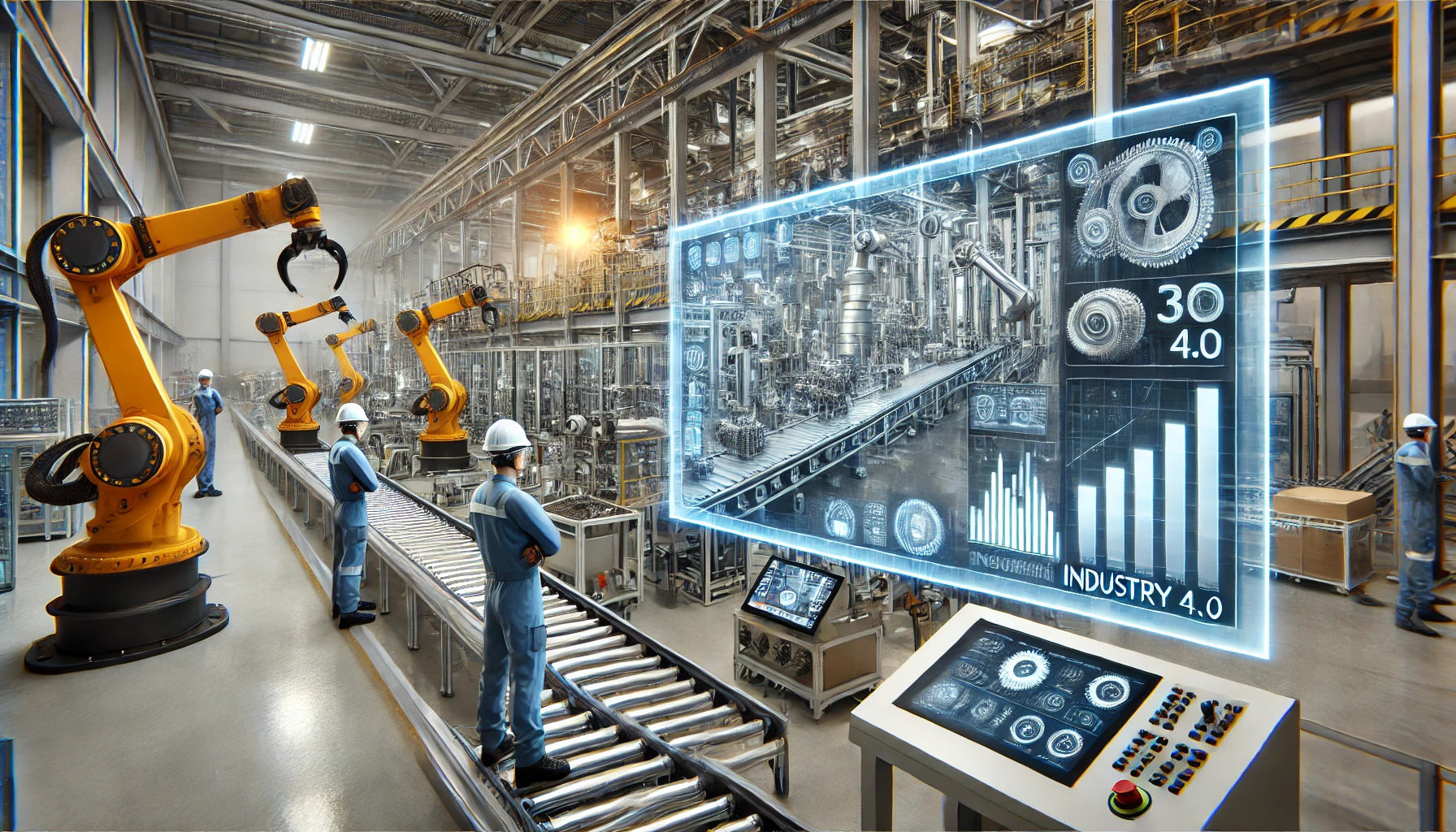
Industry 4.0 and Digital Twins: Revolutionizing Manufacturing and Beyond
Are you looking for ways to boost efficiency and cut costs in your factory? Do you want to see how cutting-edge tech can transform your entire supply chain? In this article, you will discover how Industry 4.0 and digital twins work together to reshape manufacturing and beyond.
By the end, you will learn how digital twins fit into modern production lines. You will also see how they optimize supply chains and support other innovative use cases. This knowledge can help your organization stay ahead in a fast-changing industrial landscape.
Understanding Industry 4.0
Industry 4.0 is the latest phase in industrial evolution. It uses digital technologies to connect machines, systems, and processes. The goal is higher efficiency, more flexibility, and reduced waste.
Sensors and IoT devices feed data into advanced analytics platforms. This allows real-time monitoring and better decision-making. As a result, companies can automate tasks and adapt processes on the fly.
Industry 4.0 goes beyond the factory floor. It brings together supply chains, logistics, and even product design. New business models emerge from the ability to deliver faster and smarter.
Defining Digital Twins in the Context of Industry 4.0
A digital twin is a virtual replica of a real-world product, process, or system. It mirrors physical items using real-time data. This data comes from sensors, networks, and software analytics tools.
In Industry 4.0, digital twins help companies test and adjust machines without causing downtime. They track performance and predict maintenance needs. By spotting defects early, they save both time and money.
Digital twins work with big data, AI, and IoT devices. Together, these tools create a feedback loop of continuous improvement. When combined with robotics and automation, the potential for innovation grows even larger.
Benefits of Digital Twins for Smart Manufacturing
Digital twins deliver many advantages in modern production environments. Below are some key benefits that drive their adoption.
1. Predictive Maintenance
Digital twins can detect machine wear before a breakdown. By monitoring pressure, temperature, and vibration, you can schedule repairs before costly failures occur. This boosts machine uptime and extends equipment life.
2. Faster Product Design
When engineers use a digital twin of a new machine, they can simulate stress tests and performance conditions. This speeds up the design cycle by reducing physical prototyping. In turn, it improves product quality.
3. Real-Time Monitoring
Live data feeds keep decision-makers informed about production status. They can see if a machine is running too hot or if throughput has slowed. This visibility helps teams react quickly to issues on the factory floor.
4. Cost Savings
Less unplanned downtime means higher efficiency. Digital twins also lower scrap rates by pinpointing potential defects. These savings accumulate and improve a company’s bottom line.
5. Scalability
Digital twins adapt to growing production demands. As you add more machines or expand to new locations, your digital twin network can expand as well. This approach allows smooth growth without major disruptions.
Supply Chain Optimization with Digital Twins
Supply chains involve many moving parts. Raw materials arrive from suppliers. Goods pass through manufacturing, distribution, and retail channels. Delays at any point can harm customer satisfaction.
Digital twins address this by providing:
- Enhanced Visibility
You can see where each shipment is and what condition it is in. Temperature, humidity, and other factors are monitored in real time. - Accurate Demand Forecasting
Historical data feeds machine learning models. They predict order surges or slow seasons. This helps you keep the right amount of stock and reduce waste. - Streamlined Logistics
By comparing routes and schedules in a digital environment, you can select faster or cheaper delivery paths. Changes can be made on the fly if weather or political events cause disruptions. - Risk Management
Natural disasters or supplier issues can grind operations to a halt. Digital twins allow simulations to plan for these disruptions and develop contingency strategies.
When combined with Industry 4.0 sensors, supply chain twins track products from factory to store shelf. This end-to-end approach lowers costs and improves reliability.
Other Key Use Cases Beyond Manufacturing
Digital twins are not just for factories. Their scope extends into energy, healthcare, and urban planning. Below are a few other areas seeing rapid growth in digital twin adoption:
- Smart Cities
Municipalities track traffic flow, utilities, and public transit. They then model changes to see how to reduce congestion or cut energy usage. - Healthcare
Hospitals use digital replicas of medical devices or entire wards. This allows resource allocation and real-time patient monitoring. One day, personalized digital twins of patients could guide care decisions. - Construction and Architecture
Building sites can use 3D models that update as new materials arrive or tasks get completed. This planning reduces errors and speeds up project timelines. - Automotive and Aerospace
Companies test new vehicles or aircraft engines under digital conditions. They can do virtual stress tests, predict part failures, and optimize maintenance schedules.
In each case, digital twins can boost quality, safety, and cost-effectiveness. The technology behind them continues to expand in many fields.
Real-World Example of Digital Twin Success
A leading automotive manufacturer faced frequent downtime in one of its assembly plants. These disruptions cost millions in lost output and repairs.
Engineers introduced a digital twin of the assembly line. They collected sensor data from robots and conveyor belts. Over several months, the company noticed patterns in machine strain before breakdowns.
Maintenance schedules changed to address wear at the right time. Downtime dropped by 30%, and overall throughput climbed. The digital twin also helped the firm fine-tune the line for higher speed. Eventually, they extended the same approach across multiple plants.
Steps to Implement Digital Twins in Industry 4.0
Introducing digital twins can seem challenging at first. Yet, the process becomes more manageable with the right approach. Below are some steps to guide you:
- Identify Clear Goals
Pinpoint the specific pain points or opportunities. Are you looking to reduce downtime, improve product quality, or increase speed? - Choose the Right Platform
Some tools specialize in manufacturing environments. Others focus on supply chain modeling or facility management. Select a platform that aligns with your needs. - Connect Sensors and IoT Devices
You need reliable data to feed your digital twin. Make sure to use sensors that track key metrics such as temperature, vibration, or volume. - Secure Your Data
Cybersecurity is essential in Industry 4.0. Encrypt your sensor data and control who has access to your digital twin. Always follow best practices for network security. - Pilot and Scale
Start small with one process line or a specific supply chain stage. Monitor the results, gather feedback, and optimize. Then, gradually expand the program across your entire organization.
Challenges to Consider
Digital twins in Industry 4.0 can offer impressive rewards. However, some hurdles must be addressed:
- Data Quality
If sensor data is inaccurate or incomplete, the digital twin will be flawed. Ongoing maintenance of sensors and data pipelines is crucial. - High Initial Costs
Hardware and software investments can be steep. Factor in training and hiring costs to ensure a skilled workforce. - Security Risks
More connected devices mean more points of vulnerability. A robust cybersecurity plan is key to safe Industry 4.0 adoption. - Complex Integration
Many companies have legacy systems. Integrating them with new IoT and analytics platforms can take time. Planning and gradual rollout help reduce disruptions. - Organizational Resistance
Staff may hesitate to adopt new technology. Proper training and clear communication can ease this transition.
Future Outlook: The Next Phase of Industry 4.0
Digital twins will play an even bigger role as Industry 4.0 evolves. 5G networks will boost data transfer speeds and reduce latency. This will help digital twins update in near real time, even for massive operations.
Artificial intelligence will also shape Industry 4.0. AI-enhanced models can predict complex problems faster than human experts. Robotics will advance, allowing more precise machine actions based on digital twin insights.
Edge computing will further support digital twins. Instead of sending all data to the cloud, devices can process information at the source. This approach leads to faster response times and lower bandwidth costs.
In the long run, digital twins will likely merge with emerging areas like quantum computing or blockchain. These tools can add even more security, scalability, and predictive power.
Conclusion
Industry 4.0 and digital twins form a powerful combination for businesses. They enhance production, lower costs, and reduce downtime. They also reshape supply chains and open doors to new possibilities in other sectors.
Now you have a clear view of how digital twins support smart manufacturing and supply chain optimization. You also know the steps for implementing them and the challenges to expect. By embracing these tools, your organization can stay ahead in an ever-evolving industrial landscape.
Thank you for reading. We hope this guide helps you plan your next steps in your Industry 4.0 journey. With the right strategy, digital twins can revolutionize your processes and spark exciting growth.
Author Profile
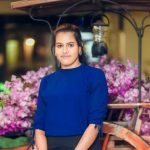
- Online Media & PR Strategist
- Hello there! I'm Online Media & PR Strategist at NeticSpace | Passionate Journalist, Blogger, and SEO Specialist
Latest entries
Robotics SimulationJune 27, 2025Why Accuracy in Robotics Simulation Is Critical Today
HPC and AIJune 27, 2025The Powerful IT Backbone Behind Urban Growth
AI PlatformJune 26, 2025AI Platforms Travel: Boost Hospitality Experience with AI
Data AnalyticsJune 23, 2025Navigating Global Asset Management Regulations Effectively