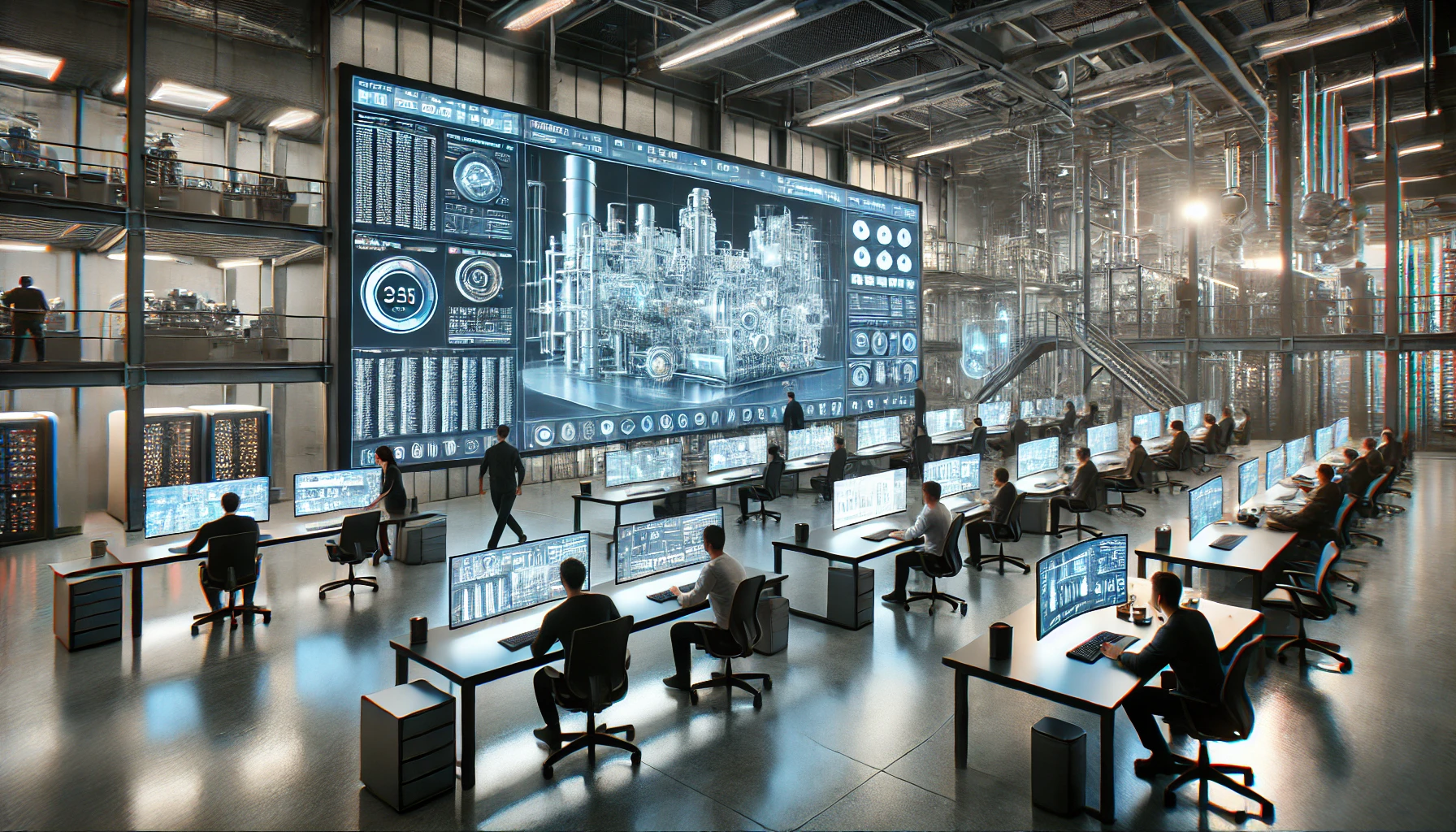
Digital Twin Basics: Understanding the Core Concepts and Benefits
Are you curious about how businesses can mirror real-world processes in a virtual environment? Do you want to know how modern organizations predict failures before they happen? In this post, you will discover the basics of digital twins, how they work, and why they matter.
Digital twin technology is gaining ground in many industries. It helps companies analyze data, simulate events, and improve products. By the end of this article, you will have a clear understanding of what digital twins are and how they can benefit your organization.
What Is a Digital Twin?
A digital twin is a virtual representation of a real-world object, process, or system. It mirrors physical items in a computer model. This model updates in real time to reflect the state of the real thing.
For example, imagine an assembly line in a factory. A digital twin would display each machine’s performance, speed, and any faults. You could then test upgrades or catch problems early without risking the actual machines.
Digital twins exist in many fields. They can model airplanes, office buildings, energy grids, or entire cities. The goal is to use real-world data to feed a precise simulation. By doing so, engineers and decision-makers can analyze outcomes and plan effectively.
How Do Digital Twins Work?
First, sensors collect data from the physical asset. These sensors measure temperature, speed, vibration, or other variables. Next, this data travels through a secure connection to the digital twin model stored on a computer or in the cloud.
Then, the model updates in real time as the physical object changes. Machine learning algorithms can further refine the model. They analyze past and present data to predict future behaviors or possible failures.
Finally, users can interact with the digital twin. They can run scenarios such as “What if the temperature rises by 10 degrees?” or “What happens if we speed up production by 20%?” The insights from these tests help optimize performance and cut costs.
Key Components of a Digital Twin
Digital twins vary depending on their purpose. Yet most digital twin platforms involve a few key components:
- Physical Asset or Process
The real-life item you want to model. This can be an engine, a factory workflow, or an entire building. - Sensors and IoT Devices
These devices gather real-time information. They measure pressure, speed, location, and other metrics. - Data Integration Layer
This layer collects sensor data and moves it to a central location. It often uses secure protocols to prevent breaches. - Digital Model
This software model mirrors the real asset. It updates based on the incoming data feed. - Analytics and Visualization Tools
These tools help you see what is happening in the model. They also let you test changes and spot potential failures. - Feedback Loop
Adjustments in the digital twin can guide real-world decisions. This loop helps refine both the physical asset and the digital model.
Benefits of Digital Twins
Digital twin technology can improve many business processes. Below are some key benefits that help explain why companies invest in it.
1. Predictive Maintenance
Maintaining machines before they fail is crucial. Digital twins let you track the health of your equipment in real time. You can foresee wear and tear and schedule repairs at the right moment. This approach helps avoid unplanned downtime.
2. Cost Savings
Virtual testing is cheaper than physical testing. You can simulate scenarios like extreme weather or peak loads without risking damage. Companies can save on materials, labor, and potential legal costs from unforeseen failures.
3. Faster Product Development
Speed to market is vital in today’s economy. Digital twins allow rapid prototyping without building many physical samples. Engineers can optimize a product design by simulating stress tests or user behavior. This method speeds up innovation cycles.
4. Better Quality Control
Data-driven insights help maintain consistent quality. If the digital twin detects issues, teams can respond quickly to correct them. This improves reliability and customer satisfaction.
5. Enhanced Collaboration
Digital twins work in a collaborative environment. Teams from different departments or regions can view the same data. This shared vision helps reduce misunderstandings and boosts decision-making.
Common Use Cases
Digital twin basics apply to a broad range of industries. Here are some popular use cases that show their versatility.
- Manufacturing
Factories use digital twins to monitor production lines. They track machine performance, materials, and worker shifts. Problems like machine malfunctions become easier to spot and fix. - Healthcare
Hospitals can create digital twins of medical devices or patient flows. This approach helps optimize device usage and plan patient care pathways. In the future, doctors may use patient-specific digital twins to personalize treatments. - Smart Cities
City planners simulate traffic flow, energy usage, and public transport. This helps them address congestion and environmental impact. Emergency services can also test response strategies for major events. - Automotive and Aerospace
Engineers model engines, transmissions, and entire vehicles. They then test them in virtual environments. This saves time on road or flight tests. It also improves safety. - Energy and Utilities
Power companies maintain digital twins of their grids. This allows them to predict and fix outages faster. Renewable energy farms also track wind or solar data for better energy output planning.
Challenges to Consider
Digital twin development has its drawbacks. It is not always simple to deploy or manage. Here are some common hurdles you might face:
- Data Quality
Digital twins depend on high-quality data. Inaccurate or missing sensor readings can damage the model’s accuracy. Ensure your data sources are reliable and well-maintained. - Complexity and Cost
Building a digital twin may require advanced software, hardware, and skilled staff. These factors increase expenses. Organizations need a clear return on investment before starting. - Cybersecurity Risks
More connected devices mean more entry points for hackers. You must secure your IoT network and stored data. Regular audits and strong encryption are essential. - Integration with Legacy Systems
Many firms still run older software that may not play well with new IoT platforms. Plan carefully to avoid connectivity issues or major tech overhauls. - Skill Gaps
Operating a digital twin involves data science, engineering, and IT skills. Some teams may need extra training or new hires. Proper planning will mitigate staffing challenges.
How to Get Started
Setting up a digital twin project can seem complicated. But the right approach makes it easier. Here are some action steps to begin:
- Define Clear Goals
Identify the specific problem you want the digital twin to solve. Are you aiming to reduce downtime, improve safety, or refine designs? Clear objectives will guide your development. - Choose Your Platform or Tools
Many providers offer digital twin platforms. Some focus on IoT data collection, while others specialize in analytics. Research options and pick the one that matches your needs. - Gather Data and Connect Devices
Install sensors on physical assets if you have not already. Next, set up reliable data pipelines. Confirm that your devices follow industry security standards. - Build and Test Your Digital Model
Model the asset or process you want to mirror. Then, run small tests to see if the data syncs properly. Refine the model as needed. - Scale Up and Integrate
Once you see positive results, expand the scope. You can add more assets or link the digital twin to other software. For instance, integrate it with inventory management or enterprise resource planning (ERP) systems. - Monitor and Improve
Digital twins are never “set and forget.” Keep refining your models. Track performance metrics and adopt updates as technology advances.
Future of Digital Twin Technology
The future of digital twins looks promising. As 5G networks spread, data transfer speeds will rise. This will allow real-time updates for even more complex systems.
Artificial intelligence will also play a key role. AI-driven models will predict failures and respond to events faster than human operators. Many companies will move their digital twin ecosystems to the cloud, ensuring they stay flexible and scalable.
Finally, edge computing may reduce latency in digital twin apps. Data processing will happen closer to where sensors collect it. This means faster feedback and more accurate responses to sudden changes.
Conclusion
Digital twins let us analyze and improve physical assets in a virtual environment. They combine sensor data, analytics, and advanced modeling to predict outcomes and guide decisions. As a result, businesses can reduce costs, optimize processes, and plan ahead.
Now that you understand the basics, you can explore how digital twin technology might benefit your organization. From predicting machine failures to simulating complex environments, the possibilities are vast. With careful planning and the right tools, you can start reaping the rewards of digital twins today.
Thank you for reading. We hope you found this explanation helpful in grasping digital twin basics. Keep this guide handy as you plan your next steps in digital twin development.
Author Profile
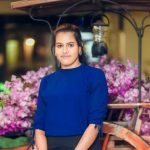
- Online Media & PR Strategist
- Hello there! I'm Online Media & PR Strategist at NeticSpace | Passionate Journalist, Blogger, and SEO Specialist
Latest entries
Conversational AIJune 20, 2025Conversational AI Security: Risks & Mitigation Strategies
Data AnalyticsJune 13, 2025Future of Data Warehousing in Big Data
AI InterfaceJune 13, 2025Aligning AI Developments with Corporate Goals in the AI Era
HPC and AIJune 13, 2025HPC Architecture Taking to the Next Level