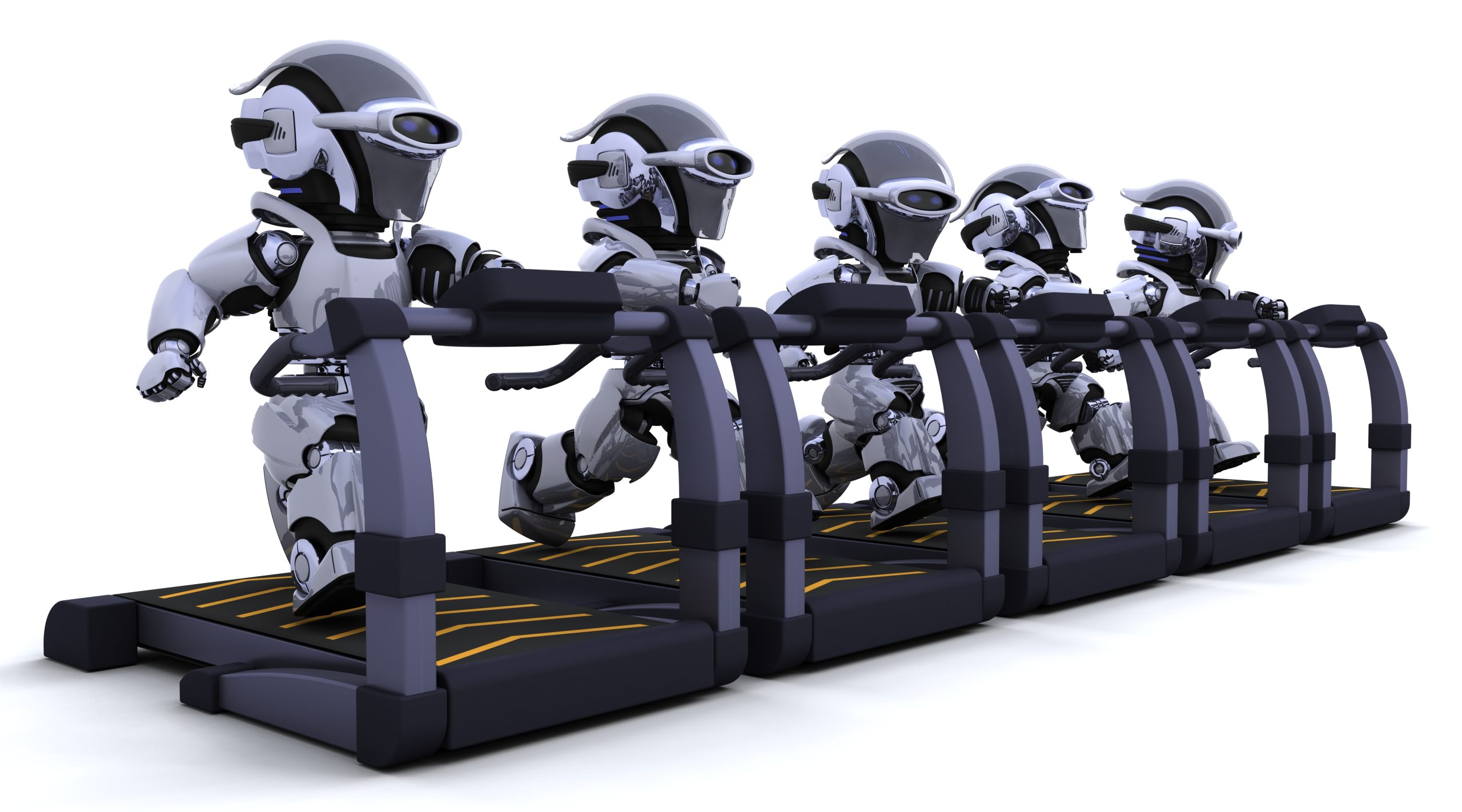
CAE for Robotics: Simulating Complex Robotic Systems
Computer-aided engineering (CAE) is changing how robots are designed and tested. It helps engineers simulate complex robotic systems before building them. This saves time, reduces costs, and boosts innovation in many industries. By the end of this article, you will learn how CAE for robotics works and why it matters.
What Is CAE for Robotics?
CAE for robotics involves using software tools to design, simulate, and analyze robotic systems. These tools give engineers a virtual environment to test their ideas. Instead of building a physical prototype, they use simulations to see how a robot might behave. This makes the development process more efficient and cost-effective.
Key Points about CAE for Robotics
1. It provides realistic simulations of robot motion and performance.
2. It identifies design flaws early and reduces risks in manufacturing.
3. It allows faster iteration, which leads to better robots.
Why Simulating Complex Robotic Systems Matters
Simulating complex robotic systems helps solve real-world problems. Robots often have moving parts, sensors, and software working together. CAE tools create digital models of these parts and predict how they interact. This approach improves accuracy and saves money by preventing design failures.
Benefits of Simulation
Reduced physical testing: Fewer prototypes mean lower costs and less wasted material.
Enhanced safety: Simulations identify potential hazards before real-world deployment.
Improved performance: Engineers can tweak and optimize designs faster.
CAE for Robotics in Various Industries
Robotic arms, drones, and autonomous vehicles all rely on CAE. Each application has unique needs, and simulations ensure that robots meet those needs. These tools help build systems for manufacturing, healthcare, agriculture, and more. By testing in a virtual space, engineers adapt the design to each industry’s standards.
Examples of Industry Applications
Manufacturing: Robots on assembly lines handle repetitive tasks with high precision.
Healthcare: Surgical robots are tested virtually to improve patient safety.
Agriculture: Automated drones and robotic harvesters are designed to withstand harsh outdoor conditions.
Designing Robotic Systems with CAE Tools
Designing a robot requires knowledge of mechanics, electronics, and software. CAE for robotics integrates all these fields into one platform. Engineers can visualize how motors, gears, and sensors will work together. This process leads to more accurate and dependable robotic systems.
Steps in the Design Process
Conceptual Modeling:Sketch out initial ideas using 3D modeling software.
Simulation and Analysis:Test the design’s strength, motion, and control system.
Optimization:Make improvements based on simulation results.
Integrating CAE for Robotics Testing
After creating a design, engineers use CAE to test it in simulated environments. They check how the robot reacts to different forces, speeds, and tasks. This stage includes stress analysis and control system validation. By identifying failures early, teams avoid costly fixes later.
Testing Techniques with CAE
Finite Element Analysis (FEA): Analyzes strength and deformation under loads.
Multibody Dynamics (MBD): Evaluates how parts move and interact in a system.
Control System Simulation:Tests how sensors and algorithms handle real-time data.
Real-World Use Cases of CAE in Robotics
Many high-tech companies already use CAE for robotics to stay competitive. For instance, drone manufacturers simulate flight patterns under different weather conditions. Warehouse automation developers test how robotic arms place items on shelves. These examples show how CAE for robotics transforms ideas into successful products.
Spotlight on Success
Autonomous Cars:Engineers simulate traffic and weather to refine self-driving algorithms.
Space Exploration: Rovers are tested in simulated lunar or Martian terrains.
Underwater Robots: Pressure and temperature effects are analyzed with virtual tests.
Challenges in Simulating Complex Robotic Systems
Despite its benefits, CAE for robotics faces some challenges. High-fidelity simulations need powerful computing resources and accurate models. Complex interactions, like collisions or fluid dynamics, require advanced software. Engineers must also verify that simulated results match real-world data.
Common Hurdles
Computing Costs:Powerful hardware is often necessary for large-scale simulations.
Model Accuracy:A flawed model can lead to incorrect conclusions.
Integration Complexity: Combining many components into one simulation can be difficult.
Future Trends in CAE for Robotics
As robotics continues to grow, CAE will evolve too. Machine learning is being introduced to make simulations smarter. Cloud-based CAE platforms are becoming popular for remote collaboration. These trends will reduce costs, speed up design, and push innovation further.
Emerging Developments
AI-Assisted Simulation: Automates repetitive tasks and aids in design optimization.
Virtual Reality (VR) Integration: Improves human-robot interface testing.
Distributed Computing: Splits simulations across multiple systems to save time.
How CAE for Robotics Drives Business Goals
The purpose of this article is to drive traffic, generate leads, and educate potential users about CAE for robotics. Companies that invest in these tools can see a faster return on investment. They reduce errors, improve product quality, and gain a competitive edge. CAE fosters efficient design cycles, which leads to better products and higher profits.
Key Outcomes
Faster Time-to-Market:Less physical testing means quicker production.
Lower Risk: Early detection of flaws prevents major setbacks.
Innovation Boost: Virtual testing encourages creative solutions.
Conclusion
CAE for robotics is transforming how we design and test robotic systems. It allows engineers to simulate complex robotic systems and catch problems early. This not only cuts costs but also improves performance and reliability. As technology advances, CAE will continue to shape the future of robotics and open new possibilities.
FAQ on CAE for Robotics
1. What is CAE for robotics?
CAE for robotics stands for computer-aided engineering. It involves using software tools to design, simulate, and analyze robotic systems before building physical prototypes.
2. How does CAE improve robot design?
It simulates different aspects of a robot’s operation. This reveals potential flaws early, saving money on physical prototypes and rework.
3. Which industries benefit most from CAE for robotics?
Manufacturing, healthcare, agriculture, and logistics all rely on robotic systems. CAE helps in each sector by improving efficiency and reducing development costs.
4. What are common challenges in simulating robotic systems?
They include high computing costs, ensuring model accuracy, and integrating multiple subsystems. Overcoming these challenges requires powerful hardware and careful model verification.
5. How is the future of CAE for robotics evolving?
It’s moving towards AI-assisted simulation, VR integration, and distributed computing. These trends will further reduce costs and speed up design cycles.
Author Profile
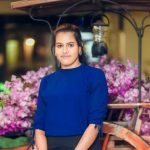
- Online Media & PR Strategist
- Hello there! I'm Online Media & PR Strategist at NeticSpace | Passionate Journalist, Blogger, and SEO Specialist
Latest entries
Scientific VisualizationApril 30, 2025Deepfake Scientific Data: AI-Generated Fraud in Research
Data AnalyticsApril 30, 2025What Is Data Mesh Architecture and Why It’s Trending
Rendering and VisualizationApril 30, 2025Metaverse Rendering Challenges and Opportunities
MLOpsApril 30, 2025MLOps 2.0: The Future of Machine Learning Operations