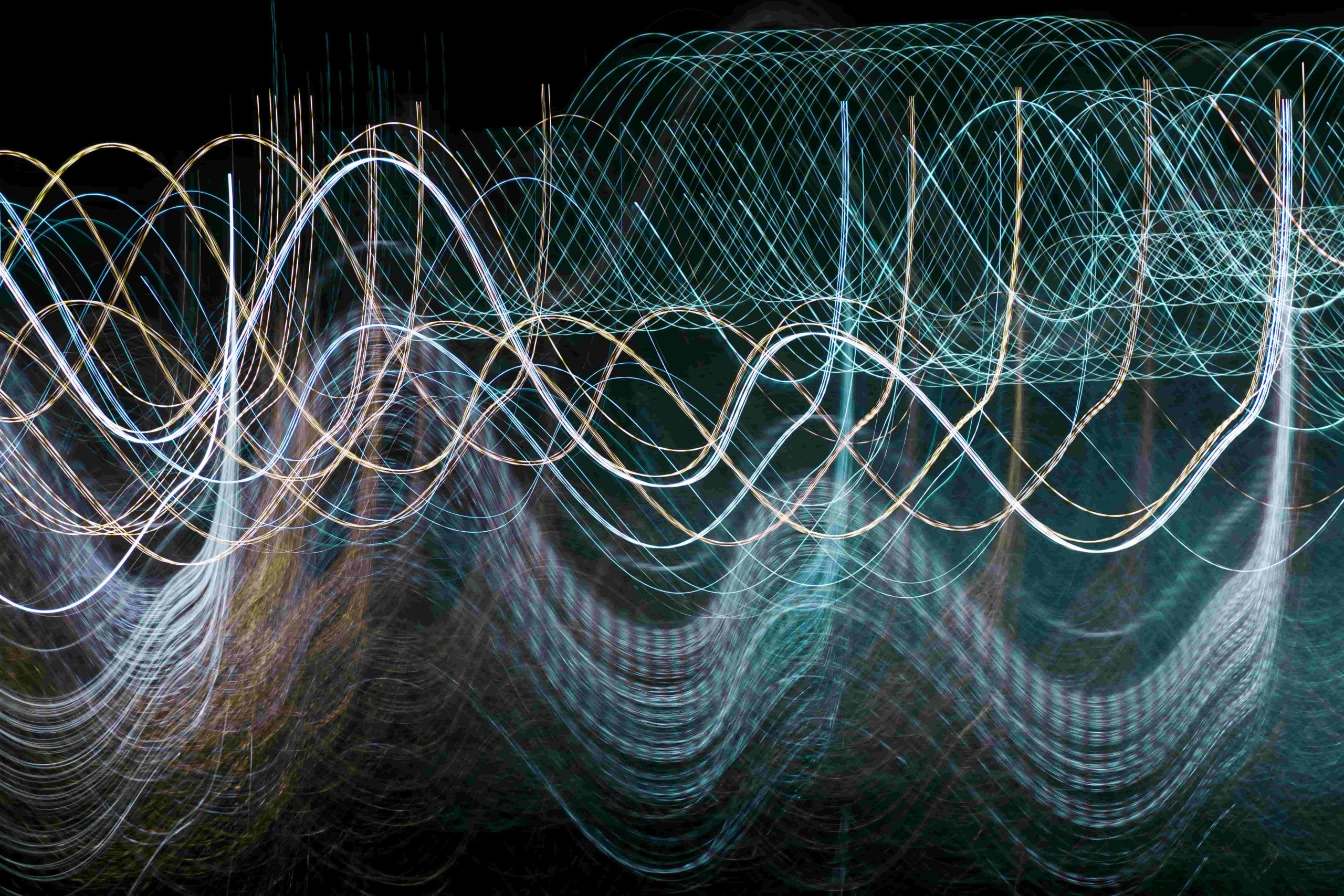
Modal Vibration Analysis: Natural Frequencies & Responses
Understanding how machines and structures behave under motion is key to building reliable systems. This is where modal vibration analysis plays an important role. In this article, you’ll learn what it is, why it’s used, and how engineers apply it to prevent failure and improve design.
By the end, you’ll know:
-
What modal vibration analysis means
-
How it helps study natural frequencies
-
Its role in preventing dangerous vibrations
-
Tools used in real-world applications
What Is Modal Vibration Analysis?
Analysis of vibrations is the process of finding the natural vibration frequencies and shapes (or modes) of an object. Every structure or mechanical part vibrates at certain frequencies when hit or moved. If energy matches a natural frequency, the object can shake dangerously even break.
This is why engineers use modal vibration analysis to design safer buildings, bridges, cars, planes, and machines.
Why Modal Vibration Analysis Matters in Engineering
Ignoring vibrations can lead to:
-
Structural failure
-
Poor performance
-
Noise and wear
-
Reduced lifespan
Analysis of vibrations helps engineers understand how a part or system will move when exposed to dynamic forces.
How Engineers Use It:
-
Testing: Hit or shake the structure with a tool and measure responses.
-
Modeling: Use software like ANSYS or MATLAB to simulate results.
-
Validation: Compare simulation and physical tests.
Key Steps in Analysis of vibrations Process
1. Identifying Natural Frequencies
This is the first goal of modal vibration analysis. Each object has natural frequencies based on its shape, size, and material.
-
Example: A guitar string has a specific sound when plucked.
-
In machines, matching vibration can damage parts or cause failure.
2. Finding Mode Shapes
Mode shapes show how the object moves at each natural frequency.
-
Some areas move more than others.
-
Visualizing this helps in improving design.
3. Damping Evaluation
Damping tells how fast the vibration fades. Less damping means more shaking.
Tools and Software for Analysis of vibrations
Engineers use both physical tools and software tools to perform analysis of vibrations.
Physical Tools:
-
Accelerometers
-
Impact hammers
-
Shakers
Software Tools:
-
ANSYS – FEA software used for vibration simulations
-
MATLAB – Useful for data analysis
-
SolidWorks Simulation – For simpler structures
These tools allow faster and more accurate analysis of vibrations, especially for complex systems.
Applications of Modal Vibration Analysis in Industries
Modal vibration analysis is used across many fields:
Aerospace
-
Airplane wings must avoid natural frequencies of wind vibrations.
Automotive
-
Ensures car engines and suspension systems don’t vibrate uncontrollably.
Civil Engineering
-
Bridges and buildings are tested for earthquakes and wind loads.
Manufacturing
-
Machines and robotic arms are checked to reduce vibration during tasks.
Benefits of Using Modal Vibration Analysis
-
Prevents resonance failures
-
Improves design efficiency
-
Reduces maintenance costs
-
Helps in troubleshooting existing systems
Best Practices for Accurate Analysis of vibrations
-
Use the correct sensor placement
-
Run tests under real working conditions
-
Compare multiple modes, not just the first
-
Always validate with both test and simulation
-
Keep damping ratios in check
For more on simulation tools, check our Generative Design CAE: Redefining Modern Engineering.
FAQs
What is modal vibration analysis used for?
It helps find natural frequencies and motion shapes of systems to avoid failure.
What tools are used in modal analysis?
Common tools include accelerometers, impact hammers, and simulation software like ANSYS.
Can modal analysis prevent equipment failure?
Yes, by identifying dangerous frequencies early, failures can be avoided.
Is modal vibration analysis only for large structures?
No, it’s used for everything from bridges to small machine parts.
Why You Should Care About Analysis of vibrations
If you’re designing anything that moves or shakes, analysis of vibrations is essential. It helps engineers understand how objects behave under force and prevents failures before they happen.
Whether you’re working in construction, aerospace, or manufacturing, investing in this analysis makes systems safer, longer-lasting, and more efficient.
Want more technical insights? Visit our engineering blog for deep dives into simulations, tools, and analysis tips.
Author Profile
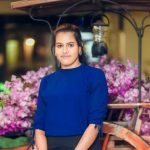
- Online Media & PR Strategist
- Hello there! I'm Online Media & PR Strategist at NeticSpace | Passionate Journalist, Blogger, and SEO Specialist
Latest entries
Computer Aided-EngineeringJuly 9, 2025Parametric Optimization Techniques for Best Design
Computer Aided-EngineeringJuly 9, 2025Modal Vibration Analysis: Natural Frequencies & Responses
NetworkingJuly 9, 2025Networking Challenges Healthcare: Key Issues & Fixes
NetworkingJuly 9, 2025Edge Computing Impact on Network Infrastructure