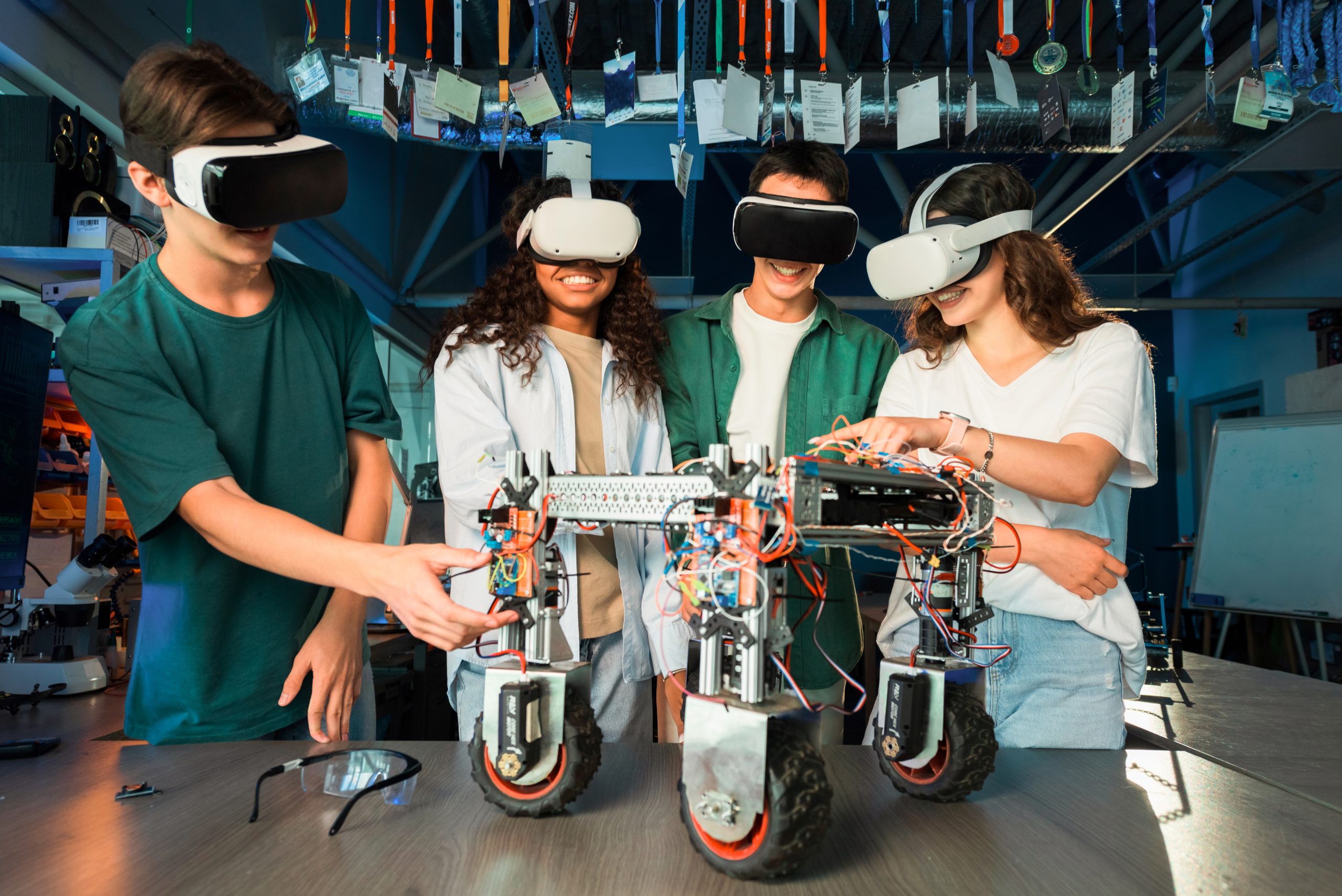
Soft robots powered by robotics simulation technology
Soft robots are flexible, adaptable, and changing how we think about automation. But how are they designed and tested before they ever touch the real world? The answer lies in robotics simulation technology.
In this blog, you’ll learn how engineers use simulation to build better soft robots. We’ll explore how this process works, its benefits, and what it means for the future of robotics.
What Is Robotics Simulation Technology?
Simulating robotics is a virtual environment where robotic systems are designed, modeled, and tested.
Unlike traditional robots with hard parts, soft robots are made from elastic materials. This makes them tricky to design because their movements are more complex and less predictable.
With simulation, engineers can:
-
Model flexible materials and how they behave
-
Test designs in different conditions
-
Save time and money by avoiding trial-and-error in the real world
Why Robotics Simulation Technology Is Key for Soft Robots
Designing soft robots by hand is slow and costly. Simulating robotics changes that by letting developers test ideas instantly.
Benefits of Using Simulation in Soft Robotics
-
Faster design cycles: Changes are made digitally without physical prototypes
-
Safer testing: Simulations reduce risks before real-world trials
-
More accurate modeling: Advanced physics engines model soft materials better
-
Cost-effective: No need for expensive physical materials in early stages
By using Simulating robotics, developers can predict how a soft robot will react to touch, heat, or pressure. This is essential for real-life uses like medical tools or wearable robots.
How Robotics Simulation Technology Supports Design and Testing
1. Digital Prototyping
Before building anything physical, designers create a virtual prototype. They use 3D modeling tools combined with Simulating robotics to see how their soft robot will move.
This lets them test:
-
Shape and structure
-
Material flexibility
-
Range of motion
2. Stress and Pressure Testing
Soft robots need to bend, twist, and stretch. Simulation helps predict:
-
How much pressure the material can take
-
Where it might tear or fail
-
How it responds under repeated movement
This saves time and helps refine materials before manufacturing.
3. Environmental Testing
Using Simulating robotics, developers can test robots in:
-
Hot or cold climates
-
Underwater conditions
-
Inside human bodies (for medical robots)
This is especially important for robots used in dangerous or sensitive environments.
Real-World Applications of Robotics Simulation Technology
Healthcare and Medicine
Soft robots are used in surgical tools and rehabilitation devices. Simulation allows:
-
Safer development of medical-grade devices
-
Accurate movement inside the human body
Wearables and Prosthetics
Wearable soft robots help people walk, move, or regain strength. Simulation improves:
-
Fit and comfort of materials
-
Real-time responses to user motion
Search and Rescue
Soft robots enter areas too dangerous for people. Simulation lets developers:
-
Train robots in unstable terrains
-
Adapt robots to tight spaces or rubble
Tools That Power Robotics Simulation Technology
Several software tools help developers model soft robots. These include:
-
SOFA Framework
-
MuJoCo
-
PyBullet
-
Unity with custom physics plugins
These tools support complex materials, soft body physics, and real-time feedback.
The Future of Robotics Simulation Technology in Soft Robotics
As computers get faster and smarter, Simulating robotics will only get better. Expect:
-
Real-time feedback during physical testing
-
AI-assisted simulation that improves design automatically
-
Cloud-based simulation for global team collaboration
This will lead to safer, smarter, and more adaptable soft robots in the coming years.
FAQ
Q1: Why use simulation for soft robots?
A: Soft robots are hard to predict physically. Simulation lets developers model and test designs safely.
Q2: What materials are used in soft robots?
A: Common materials include silicone, rubber, and other flexible polymers.
Q3: Are simulation tools expensive?
A: Some tools are open-source (like SOFA), while others are commercial. Cost depends on project size and needs.
Q4: Can simulation fully replace real testing?
A: No, but it greatly reduces the time and cost before building physical prototypes.
Q5: What industries use soft robots?
A: Healthcare, rescue operations, manufacturing, and wearable tech.
The Power of Simulation in Soft Robotics
Simulating robotics is changing how we build soft robots. By testing designs virtually, engineers can move faster, reduce costs, and create safer robots for real-world use.
This technology is essential for the future of flexible robotics, and it’s only going to become more important.
Author Profile
- Hey there! I am a Media and Public Relations Strategist at NeticSpace | passionate journalist, blogger, and SEO expert.
Latest entries
Digital Twin DevelopmentAugust 23, 2025Data Wrangling Twins Guide: Clean IoT Data for Digital Models
NetworkingAugust 22, 2025Network Digital Twin Technology for Smarter IT Systems
Vehicle SimulationAugust 22, 2025Simulating Second-Life EV Battery Performance Insights
HPC and AIAugust 22, 2025Hyperparameter Optimization Scale Strategies